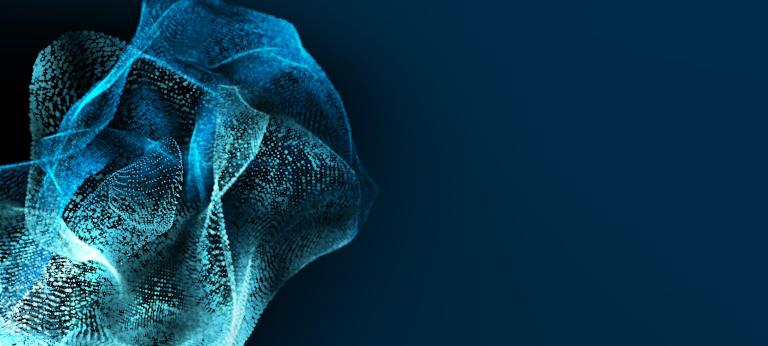

Erfolgreich in den 2020ern: Fünf Herausforderungen für COOs
Mehr Effizienz durch funktionale Ausrichtung, Automatisierung und Modularisierung
Fast jede Branche kennt das Problem: Technologische, regulative und marktseitige Trends sorgen dafür, dass die Produktentwicklung ständig aufwändiger und teurer wird. In der Automobilindustrie kamen deshalb zuletzt bereits die Gewinnmargen unter Druck, aber auch andere Branchen sind gebeutelt. Vor allem fünf Faktoren sind maßgeblich dafür verantwortlich, dass die Entwicklungsbudgets der Unternehmen immer häufiger überschritten werden.
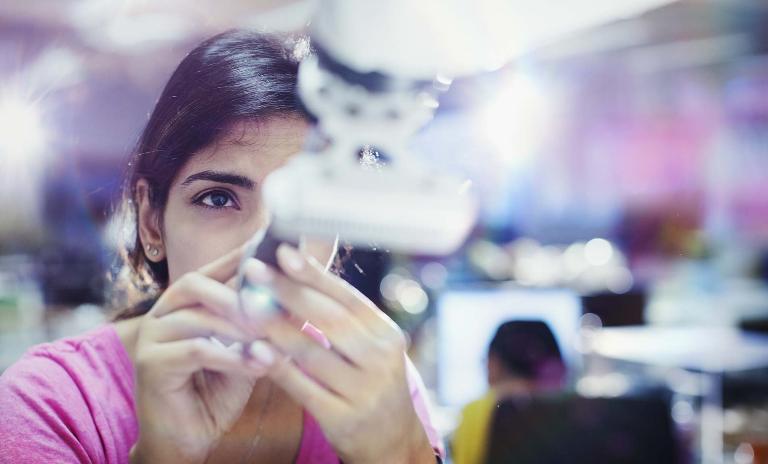
"Die wettbewerbsfähige Entwicklungsabteilung der Zukunft erfüllt drei Bedingungen: Sie arbeitet funktionsorientiert, bringt Produkte schnell und in möglichst effizienter Variantenvielfalt auf den Markt und beherrscht Systemkomplexität."
1. Der Zwang der Zweigleisigkeit: Technologien müssen simultan entwickelt und aufrechterhalten werden
Markantestes Beispiel hierfür ist die Entwicklung in der Automobilindustrie. Ging man in der Branche lange davon aus, dass Elektroantriebe den Verbrennungsmotor früher oder später ablösen, gilt inzwischen als sicher, dass beide Technologien mindestens für die nächsten 20 Jahre parallel aufrechterhalten und weiterentwickelt werden müssen. Die Folge: Entwicklungsabteilungen benötigen zusätzliches Personal, Portfolio- und Systemkomplexität steigen, ebenso die Applikationsaufwände.
Doch nicht nur die Automobilhersteller leiden. Der Umstieg von „konventionellen“ Technologien wie Hydraulik oder Pneumatik auf elektrische und elektronische bzw. digitale Technologien beschäftigt derzeit viele Branchen. Die Gleichzeitigkeit verschiedener Technologiekonzepte erschwert die Situation zusätzlich. Und sie treibt die Kosten, auch und gerade in der Entwicklung. Auch in der Bahnindustrie hat sich mit dem druckluftfreien „Airless Train“ eine Paralleltechnologie etabliert, auf die sich Zulieferer technologisch einstellen müssen. Das heißt, sie müssen die Entwicklung von elektromechanischen Bremsen so weit vorantreiben, dass auch die erforderlichen Redundanzsysteme ohne Druckluft auskommen. Nicht zuletzt ist dies aufgrund der hohen Sicherheitsanforderungen auch mit dem Gesetzgeber abzustimmen.
Fraglich bleibt aber, ob sich der Airless Train mittelfristig als führende Technologie weltweit durchsetzen wird. Selbst wenn, wird dies Jahrzehnte noch dauern – nicht zuletzt wegen des sehr langen Lebenszyklus´ von Zügen. Bahnzulieferer stehen damit vor der Herausforderung, druckluftfreie und herkömmliche Systeme parallel zu bedienen. Für beide brauchen sie entsprechend qualifizierte Mitarbeiter, Vorentwicklungsprojekte, Kapazitäten für Prototypen und Testing sowie besondere Verfahrenstechniken.
2. Das Ende des mechanischen Zeitalters: Integration von Mechanik, Elektrik, Elektronik und Software
Elektrifizierung, Autonomie und Vernetzung, etwa durch die zunehmende Verbreitung von IoT-Devices, sind eine wichtige Voraussetzung für den Produkterfolg. Denn die Funktionalität spielt inzwischen eine weitaus größere Rolle als die physischen Komponenten eines Produkts. Vor allem die Systemintegration ist in diesem Zusammenhang ein neuralgischer Punkt in der Entwicklung, der die Kosten schnell in die Höhe steigen lässt. So erfordert beispielsweise die zunehmende Autonomie von Maschinen und Fahrzeugen ein systemisch einwandfreies Zusammenspiel verschiedenster Komponenten, etwa der Sensorik mit Lenkung, Bremse und Achse. Reines „Komponentendenken" ist daher nicht mehr zielführend.
Auch das veränderte Verhalten und die Erwartungen von Nutzern führen häufig dazu, dass die traditionelle Mechanik durch andere Technologien ersetzt wird. So kann der bequemste Weg, ein Schloss zu öffnen, eine App statt eines Schlüssels sein. Dafür jedoch muss die Mechanik des Schlosses mit Elektrik, Elektronik und Software kombiniert werden. Softwareintegration in mechanische Komponenten spielt überdies aus kaufmännischen Gründen eine Rolle. Gebremst werden Züge und Autos heutzutage nicht mehr allein durch Mechanik oder Pneumatik, sondern softwaregestützt über Algorithmen, um auf diese Weise auch den Verschleiß und die "Total Cost of Ownership" zu reduzieren.
Aus (mechanischen) Komponenten werden also mehr und mehr (mechatronische) Systeme. Bislang mechanisch geprägte Zulieferer stehen nicht nur vor der Aufgabe, neue Kompetenzen in den für sie eher unbekannten Disziplinen Elektrik, Elektronik und Software aufzubauen, sondern müssen auch ihren gesamten Produktentstehungsprozess und die dahinterstehende Produktarchitektur überdenken.
3. Papierkrieg in der Entwicklung: Steigender Dokumentationsaufwand bindet Ressourcen
Das Thema Dokumentation nimmt im gesamten Produktentstehungsprozess einen immer größeren Raum ein. Das hängt unter anderem damit zusammen, dass nicht nur Funktionalität und Qualität eines Produktes getestet werden, sondern dass auch die Entstehung an sich regulatorisch immer stärkere Nachverfolgung notwendig macht. Dies wiederum dient in Zeiten steigender Autonomisierung vor allem der rechtlichen Absicherung der funktionalen Sicherheit. Denn zwar nehmen autonome Maschinen und Fahrzeuge dem Nutzer künftig mehr und mehr Entscheidungen ab, im Falle eines maschinellen Fehlverhaltens und daraus resultierenden Unfällen wird allerdings der Hersteller verantwortlich gemacht.
Bei der Dokumentation des Entwicklungsprozesses unterliegen Unternehmen strengen regulativen Anforderungen. Im Prozessstandard SPICE etwa werden spezielle Prozessanforderungen gestellt, die für eine Zertifizierung erfüllt sein müssen. In der Automobilindustrie sorgt das bei vielen Zulieferern für erhebliche Kopfschmerzen, denn an der "A-SPICE-Konformität" und der damit verbundenen Zertifizierung hängen millionenschwere Aufträge.
Ein Rückgang des Dokumentations- und Absicherungsaufwands in der Produktentwicklung ist – zum Leidwesen von Unternehmen und betroffenen Mitarbeitern – nicht absehbar. Ingenieurinnen und Ingenieure werden also weiterhin mit administrativen Aufgaben von ihrer eigentlich wertschöpfenden Arbeit in Konstruktion, Design oder Testing abgehalten.
Der steigende administrative Aufwand ist aber auch ein maßgeblicher Aufwands- und Kostentreiber in den Entwicklungsabteilungen der Industrie. Angesichts der oftmals versprengten, schnittstellenreichen Toollandschaft sind die Entwicklungsabteilungen stark mit händischer Dateneingabe, -übertragung und -pflege beschäftigt. Viel Zeit wird drüber hinaus auf die Erstellung von Präsentationsunterlagen verwendet. Der administrative Aufwand summiert sich schnell auf 20 bis 30 Prozent der Arbeitszeit von Entwicklerinnen und Entwicklern – despektierlich wird in diesem Zusammenhang deswegen auch gerne von „Powerpoint-Ingenieuren“ gesprochen.
4. Schwieriger Spagat: Mit den Kunden- und Marktanforderungen wachsen Applikationsaufwände und Variantenvielfalt
Sowohl die Globalisierung als auch der in jüngster Zeit wieder steigende Protektionismus lassen die Zahl der Ländervarianten immer weiter steigen, denn in jedem Markt gelten unterschiedliche regulatorische Rahmenbedingungen. Viele Unternehmen geraten dadurch in eine Zwickmühle: Entweder müssen sie die kostspielige Entwicklung einer Ländervariante auf sich nehmen, um den dortigen gesetzlichen Anforderungen gerecht zu werden, oder der entsprechende Markt muss komplett von der Vertriebslandkarte gestrichen werden.
Strategische Überlegungen zur Eindämmung der Varianten- und Applikationsvielfalt mutieren rasch zum Kräftemessen der Unternehmensbereiche: Während die Entwicklungsleiterinnen und -leiter ihre Budgets aus allen Nähten platzen sehen und deswegen dringend für eine Reduktion von Ländervarianten werben, fürchten die Kollegen vom Vertrieb dahinschmelzende Absatzvolumina.
Grundsätzlich lässt sich das Problem, dass das Produktspektrum mit der Bandbreite der globalen Kundenanforderungen immer weiter wächst, kaum auflösen. Die Kluft zwischen High-End-Lösungen und Standardprodukten ist einfach zu groß geworden. So fehlt etwa bei Industriegütern in Emerging Markets häufig die Infrastruktur, um beispielsweise Produktionsmaschinen zu vernetzen. Damit sind einige teure Funktionen für die dortigen Kunden gar nicht nutzbar und das Produkt gemessen am kundenwahrnehmbaren Mehrwert zu kostspielig. In westlichen Märkten dagegen sind diese Funktionen zwingend erforderlich, um die Technologieführerschaft zu behaupten. Bekannt ist auch, dass asiatische Endkunden deutlich preissensibler sind. Das erhöht die Nachfrage nach günstigeren Standardlösungen zulasten teurer High-End-Lösungen. Hersteller stehen vor der Herausforderung, dieses breite Spektrum möglichst komplexitätsarm zu managen. Für viele ist es eine Zerreißprobe zwischen dem „Blue Ocean“ der Technologieführerschaft und dem „Red Ocean“ kommoditisierter, kostenführender Projekte.
5. Fast forward im PEP: Druck auf Time-To-Market steigt weiter
Produktlebenszyklen werden immer kürzer, bedingt unter anderem durch kürzere Lebenszyklen einzelner Komponenten wie Displays oder Connectivity-Systemen. Ursächlich hierfür ist weniger die eigentliche „Haltbarkeit" der Produkte als die Tatsache, dass Produktverbesserungen schneller in den Markt kommen. Vor allem im Bereich Consumer Electronics sinken die Nutzungsdauern beim Kunden immer weiter: Einerseits befeuern technische Neuerungen und verbesserte Produktreleases – etwa bei Smartphones – die Nachfrage der Kunden, andererseits zwingen häufige Änderungen an den Schnittstellen wie Mini-/ Mikro-USB, USBC etc. die Konsumenten durch die entstehenden Inkompatibilitäten zum Modellwechsel. Ähnlich hochfrequente technologische Innovationen erwarten Kunden auch in ihrer User Experience mit anderen Produkten in ihrem Umfeld, vom Auto bis zur Waschmaschine.
Eines haben alle fünf genannten Entwicklungen gemeinsam: Werden Organisation, Prozesse, Systeme und Ressourcen nicht achtsam entsprechend ausgelegt, galoppieren die Entwicklungsaufwände schnell davon. Denn noch schneller mehr von dem zu entwickeln, was teilweise außerhalb des jahrzehntelang bearbeiteten Kompetenzprofils liegt, ist alles andere als trivial. Und nicht zum Nulltarif zu haben.
Nach vorn geschaut: Welche Schritte sind nötig für "Next Level Engineering"?
Werfen wir nun den Blick auf mögliche Lösungsansätze. Vor überzogenen Erwartungen sei dabei schon vorab gewarnt: Mit einfachen "Quick Wins" sind die skizzierten Herausforderungen nicht aus der Welt zu schaffen.
Mit zukunftsfähigen Strukturen Silos durchbrechen und Innovationen fördern
Entwicklungsfunktionen, die sich an physischen Komponenten orientieren – etwa die "KEFAG"-Logik bei Automobil-OEMs – haben langfristig wahrscheinlich ausgedient. Ihre Organisationsstruktur muss sich stattdessen an Funktionen ausrichten und deutlich durchlässiger werden. Das heißt: Team- und Projektstrukturen statt starrer Abteilungssilos, bereichsübergreifende Zusammenarbeit mit effizienter Kommunikation und digitalen Workflows.
Entscheidend ist es hierbei nach unserer Erfahrung, auch leistungsfähige informelle Kanäle der Zusammenarbeit zu schaffen, die insbesondere Mitarbeiter an verschiedenen Standorten – und sei es nur im Gebäude nebenan – verbinden. So war etwa die Kaffeeküche schon häufig die Geburtsstätte neuer Patente. Das vermeintliche ziellose Miteinander der Kolleginnen und Kollegen ist ein nicht zu unterschätzender Nukleus für die Kreativität und Innovationskraft von Unternehmen. In virtuellen Teams können „digitale Kaffeeküchen" geschaffen werden, etwa in Form von Corporate Social Media.
Mit Automatisierung administrativer Aufgaben Zeit freischaufeln
Noch profitieren erst wenige Unternehmen von den Möglichkeiten, die die Automatisierung von administrativen Tätigkeiten auch in der Entwicklung bietet, etwa durch Robot Process Automation (RPA) und automatisierte Lastenheftanalyse. Doch mittelfristig wird es sich niemand leisten können und wollen, dass sich die Mitarbeiter zu etwa einem Viertel ihrer Zeit mit administrativen Tätigkeiten beschäftigen, statt Produkte zu entwickeln, zu testen und zu validieren. Insbesondere Dateneingaben, die aufgrund fehlender Schnittstellen von einem System ins andere übertragen oder in Excel-Tabellen dokumentiert werden müssen, sollten in den kommenden zehn Jahren der Vergangenheit angehören.
Robot Process Automation-Lösungen können sich wiederholende Prozesse und Aufgaben automatisiert übernehmen. Dabei müssen sie nicht aufwendig „angelernt“ werden, sondern ahmen menschliche Interaktionen mit Benutzerschnittstellen von Softwaresystemen schnell und einfach nach. So entlasten sie Anwender von repetitiven, wenig wertstiftenden und vor allem wenig zufriedenstellenden Tätigkeiten und schaffen Freiraum für die wesentlichen Aufgaben.
Systemkomplexität beherrschbar machen durch neue Kompetenzen und eine tragfähige Architektur
Entwicklungsabteilungen der traditionell geprägten mechanischen Industrie brauchen mehr Systemverständnis bei den Mitarbeitern, vor allem mehr kritische Kompetenz in den Bereichen Elektrik, Elektronik und Software. Der viel zitierte „War for Talents“ kommt hier zum Tragen – vor allem auch, weil die benötigten strategischen Kompetenzprofile für die traditionellen Industrieunternehmen schwer zu umreißen sind. In vielen Fällen wird daher mit externen Entwicklungsressourcen gearbeitet, um akute "Brände" zu löschen". Diese kurzfristige Orientierung geht allerdings zulasten einer strategisch orientierten Wertschöpfungsstrategie.
Bei der Rekrutierung der genannten Profile müssen die Industrieunternehmen eingetretene Pfade verlassen und deutlich mutiger agieren. Das heißt beispielsweise, auch international zu rekrutieren, selbst wenn die fehlenden Sprachkenntnisse zunächst ein Hindernis darstellen, oder ganz neue Zielgruppen ansprechen. Das Image deutscher Unternehmen, die für 35 Stunden-Wochen und 30 Tage Urlaub bekannt sind, garantiert längst keine einfache Kandidatensuche mehr. Doch selbst wenn die umkämpften Köpfe erfolgreich an Bord sind, ist die Arbeit nicht zu Ende. Die verschiedenen Bereiche müssen schließlich auch miteinander verzahnt werden, „tickt" ein Softwareingenieur doch bekanntermaßen völlig anders als etwa ein „klassischer" Maschinenbauingenieur.
Einmal mehr sind die Zulieferer hier besonders gefordert, denn OEMs gehen branchenübergreifend dazu über, die Systemkompetenz in ihren Lastenhefte n an die Lieferanten abzugeben. Damit wird nicht nur das Systems Engineering der eigenen Komponente, sondern auch die Integrationsfähigkeit in das System des OEMs zum zentralen Wettbewerbsfaktor.
Neben dem veränderten Kompetenzprofil der Belegschaften ist die Produktarchitektur ein zentraler Hebel, um die Komplexität von Systemen besser beherrschbar zu machen – statt von ihnen beherrscht zu werden. Das zentrale Stichwort hier lautet Modularisierung. Obwohl seit vielen Jahren diskutiert, wagen sich Techniker nach unserer Erfahrung nicht konsequent genug an diese Aufgabe heran. Das hat seinen Preis: insbesondere im Anlagenbau wird das mit Engineered-to-order-Anteilen von bis zu 40%[1] des Auftragsvolumens offenkundig. Denn mit zunehmender Dominanz mechatronischer und softwaregestützter Systeme steigt der Validierungsaufwand von Systemen exponentiell mit deren Komplexität. Wird nur ein „Puzzleteil" im System verändert, muss ein nicht-modulares System stets komplett neu validiert werden. Dabei wäre es wesentlich effizienter, eine Referenzvalidierung der Module zu nutzen.
Permanente Anpassungsfähigkeit sicherstellen mit OPERA
Das im Beitrag beschriebene Next Level Engineering ermöglicht Unternehmen, den Prozess der Produkt- und Dienstleistungsentwicklung mit Technologien wie künstlicher Intelligenz, robotischer Prozessautomatisierung (RPA), digitalen Zwillingen im Engineering und Virtual Reality zu beschleunigen und zu verbessern. All diese digitalen Technologien ergänzen die Funktionen um zusätzliche Dimensionen der Anpassungsfähigkeit. Sie erhöhen nicht nur die Erfolgsquote von Produkt- und Dienstleistungsinnovationen, sondern helfen am Ende auch dabei, Zeit und Geld zu sparen.
Die skizzierten Lösungsansätze sind Teil des strategischen Gesamtkonzepts, das wir OPERA nennen. OPERA steht für Open up Operations, Perfect the value chain, Embrace digital, Reorchestrate value generation und Accelerate the learning game und beschreibt als strategisches Gesamtkonzept den Rahmen für zukunftsfähige Operations.
Kontakte
Möchten Sie mehr über die Herausforderungen für COOs erfahren? Kontaktieren Sie unsere Experten Carsten Bock und Laura Jacobey .