Roland Berger hat für produzierende Unternehmen, die ihre Fertigung wettbewerbsfähig aufstellen wollen mit dem Next Generation Manufacturing Framework ein breites Spektrum an zukunftsorientierten Beratungsdienstleistungen entwickelt.
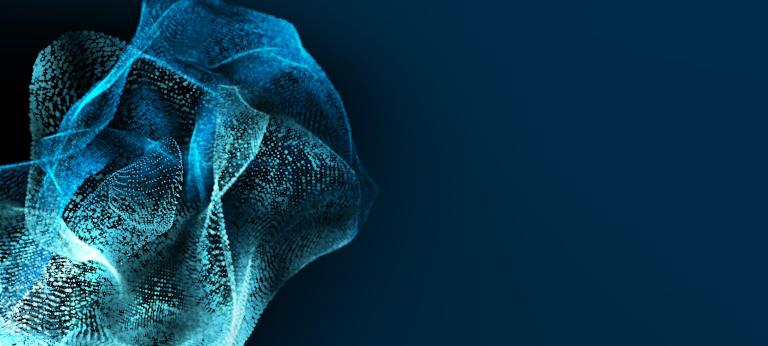

Globale Trends fördern Umdenken in der Produktion und bieten Chancen zur Steigerung der Wettbewerbsfähigkeit
Zukunftsfeste Produktion: Next Generation Manufacturing als Lösung, wo traditionelle Effizienzhebel versagen
Mit über 6500 Unternehmen, rund einer Million Mitarbeitern und einem Umsatz von gut 220 Milliarden Euro ist der deutsche Maschinen- und Anlagenbau neben der Automobilindustrie der größte Industriezweig hierzulande. Doch auch er erlebt einen Wandel, der sich aus weltweiten Entwicklungen ergibt: Gestörte Lieferketten und steigende Logistikkosten, geänderte Anforderungen von Kunden, Investoren und Gesetzgebern in Bezug auf Nachhaltigkeit und Produktionsstandorte, mehr Nachfrage nach individualisierten Produkten, technische Disruptionen – die Einflüsse auf die Unternehmen sind vielfältig. All diese Trends erfordern von den Unternehmen Anpassungen, wenn sie einen langsamen und stetigen Niedergang vermeiden wollen. Gleichzeitig bieten sie aber auch die Chance, die Branche zu transformieren und die Produktion neu aufzustellen. Vor diesem Hintergrund haben der VDMA und Roland Berger eine Umfrage unter den VDMA-Mitgliedsunternehmen durchgeführt und so ein Stimmungsbild im deutschen Maschinen- und Anlagenbau erfasst. Die Ergebnisse zeigen: Die traditionellen Hebel zur Kostensenkung und Effizienzsteigerung sind vielfach ausgereizt, doch es gibt neue Ansätze, mit denen sich die aktuellen disruptiven Trends nutzen lassen, um die Branche zukunftsfest aufzustellen.

Mit seinem hohen Exportanteil sowie vielen Zulieferern in aller Welt profitierte der Maschinenbau jahrzehntelang vom globalen Handel. Niedrige Logistikkosten und gut eingespielte Lieferketten erlaubten den Unternehmen, dem alltäglichen Kosten- und Effizienzdruck zu entkommen, indem sie die Herstellung bestimmter Komponenten in Niedriglohnländer verlagerten sowie die Produktivität in ihren eigenen Herstellungsprozessen durch verstärkte Automatisierung, Optimierung und Methoden wie den "Lean-Ansatz" steigerten. Doch dieses System wird in jüngster Zeit durch eine Reihe von Entwicklungen infrage gestellt, die ein Weiter-so unmöglich machen. Im Zentrum stehen dabei die Auswirkungen von sechs zentralen Trends , die den Wandel vorantreiben:
- Nachhaltigkeit gewinnt zunehmend an Bedeutung und wird von Verbrauchern, Investoren und Regierungen gleichermaßen eingefordert.
- Technologische Umbrüche wie das nahende Ende von fossilen Antriebs- und Stromerzeugungstechnologien stellen ganze Geschäftsmodelle infrage.
- Der Standort der Produktion wird wichtiger, da Transport- und Logistikkosten sowie Lieferketten-Risiken zunehmen und lokale Produktion von Kunden gewünscht und von Regierungen gefordert wird.
- Individualisierte Produkte und Einzelanfertigungen sind zunehmend gefragt und sorgen für mehr Komplexität in der Herstellung.
- Populismus ist in immer mehr Ländern ein Thema und zwingt viele Unternehmen, mehr auf ihre öffentliche Wahrnehmung sowie die ihrer Produkte und auf das Setup Ihres Produktionsnetzwerkes zu achten.
- Digitalisierung und Industrie 4.0 haben den Point of no return überschritten und gewinnen immer mehr Bedeutung in der industriellen Produktion.
All diese Entwicklungen weisen in dieselbe Richtung und erfordern von produzierenden Unternehmen Anpassungen. Andererseits bieten sie den Herstellern aber auch die einmalige Gelegenheit, ihre Branche zu transformieren und die Produktion auf ein neues Level zu heben.
"Mit NGM können Unternehmen ihre Produktion von der 'lästigen Verpflichtung' in einen Werttreiber und entscheidenden Wettbewerbsvorteil verwandeln."
Unternehmen erwarten weiter steigenden Kostendruck in der Produktion
Die Umfrage von Roland Berger und dem VDMA ergibt ein klares Bild: 80 Prozent der Maschinenbauunternehmen sehen ihre Produktion unter einem permanent hohen Kosten- und Effizienzdruck ; 64 Prozent erwarten, dass dieser in Zukunft weiter steigt (Slider-Bild 1). Am stärksten betroffen fühlen sich dabei Unternehmen aus dem Fachverband Antriebstechnik: Hier gibt es weniger Differenzierungspotenzial und daher einen größeren (Preis-)Wettbewerb.
Gegen den Kosten- und Effizienzdruck haben die befragten Unternehmen bisher vor allem traditionelle Hebel eingesetzt: Sie versuchen, Prozesse weiter zu optimieren und zu automatisieren, vergeben Teile der Produktion nach außen oder verlagern sie in Länder mit niedrigeren Löhnen, streben schlankere Wertschöpfungsketten an usw. (Slider-Bild 2). Doch es zeigt sich auch, dass immer mehr Unternehmen erkannt haben, dass diese „alte Welt“ so nicht mehr funktioniert: Eine Mehrheit der Befragten hält es für zunehmend schwierig, mit den traditionellen Methoden weitere Fortschritte zu erreichen – das Potenzial der bisherigen Hebel ist erschöpft. Dazu kommt: Wenn alle Wettbewerber auf die gleichen Optimierungsrezepte setzen, bleiben kaum Möglichkeiten, sich zu differenzieren: Nur 7 Prozent der Befragten sehen hier noch genügend Spielraum.
Next Generation Manufacturing als Weg aus der Sackgasse
Diese und weitere Umfrageergebnisse zeigen, dass produzierende Unternehmen neue Wege gehen müssen, um aus der Sackgasse der „alten Welt“ herauszukommen. Dafür hat Roland Berger das Konzept Next Generation Manufacturing (NGM) entwickelt: Damit können Unternehmen entlang der oben genannten sechs Trends individuell passende Maßnahmen erarbeiten, um mit den neuen Herausforderungen umzugehen. NGM beruht dabei vor allem auf einer neuen Denkweise und umfasst ein ganzes Bündel von Ansätzen, mit denen Unternehmen sich die „neue Welt“ erschließen können, in der Produktion keine „lästige Verpflichtung“ mehr ist, sondern ein Werttreiber und entscheidender Wettbewerbsvorteil.
Viele Unternehmen haben das Potenzial bereits erkannt, das sich daraus ergibt: 59 Prozent der Umfrageteilnehmer sehen Chancen für mehr Wettbewerbsfähigkeit, wenn sie die sechs NGM-Trends in ihrer Produktionsstrategie berücksichtigen. 57 Prozent glauben, dass sie damit ihre Produktion neu denken und aufstellen können. Allerdings fühlen sich umgekehrt viele noch unsicher: Nur knapp ein Viertel hält sich selbst für gut aufgestellt und glaubt, beim Thema NGM eine Vorreiterrolle spielen zu können. Ein Manko sind dabei auch die Rahmenbedingungen von staatlicher Seite: 68 Prozent der befragten Unternehmen sieht hier Mängel, insbesondere bei rechtlichen Themen wie dem Schutz geistigen Eigentums, der Korruptionsbekämpfung und dem Bürokratieabbau, technischen Themen wie dem Zugang zu schnellem Internet, einer stabilen Stromversorgung und der Transportinfrastruktur und steuerlichen Aspekten wie Zöllen, der öffentlichen Forschungsförderung und den Einkommensteuern; dazu kommen weitere Themen wie Ausbildung und Fachkräftenachwuchs oder öffentliche Sicherheit (Slider-Bild 4).
Best Practice Beispiele belegen das Potenzial von NGM
Als Teil der Studie führten die Experten von Roland Berger und dem VDMA auch ausführliche Interviews mit Unternehmen, die als Pionier beim Thema NGM gelten. Hier zeigte sich erneut, dass das Konzept kein standardisiertes System ist, sondern ein vielfältiger Werkzeugkasten, aus dem jedes Unternehmen individuell die für sich passenden Elemente auswählen und angepasst umsetzen muss. So konzentriert sich ein global führender Anlagenbauer vor allem auf den Trend Digitalisierung und hat unter anderem seine gesamte Wertschöpfungskette vom Zulieferer über die Montage bis hin zum Aftersale-Service digital integriert. Heute werden Bestellvorgänge automatisiert und digital abgewickelt – bei rund 1000 Zulieferern und jährlich 600 Millionen Teilen ergibt sich daraus ein erheblicher Effizienzgewinn.
Ein anderes Unternehmen, Traditionshersteller von Pumpen, hat in den vergangenen sieben Jahren am deutschen Stammsitz eine komplett neue Smart Factory errichtet und damit den deutschen Produktionsstandort gestärkt. Neben den auf Nachhaltigkeit optimierten Gebäuden und Infrastrukturen wurden dazu auch die Produktionsprozesse neu aufgestellt: Von der Planung der Kundenaufträge, über eine automatisierte Produktion und dynamisch gesteuerte Logistikprozesse bis hin zur Einbindung der Zulieferer sind heute sämtliche Abläufe durchgehend digitalisiert. Das erlaubt zum Beispiel flexible Reaktionen auf Nachfrageänderungen, zudem können Kunden ihr individuelles Produkt selbst online konfigurieren, per Knopfdruck bestellen und so den automatisierten Produktionsprozess anstoßen. Bilanz gut zwei Jahre nach Fertigstellung der neuen Smart Factory: Material- und Lagerbestand gesunken, Produktionszeiten verkürzt – bei einer um rund 10 Prozent gestiegenen Produktivität.
Die gemeinsame Studie von VDMA und Roland Berger mit weiteren Ergebnissen sowie den Praxisbeispielen wird voraussichtlich Ende Juni veröffentlicht.
Registrieren Sie sich jetzt, um regelmäßige Einblicke rund um das Thema "Next Generation Manufacturing" zu erhalten.