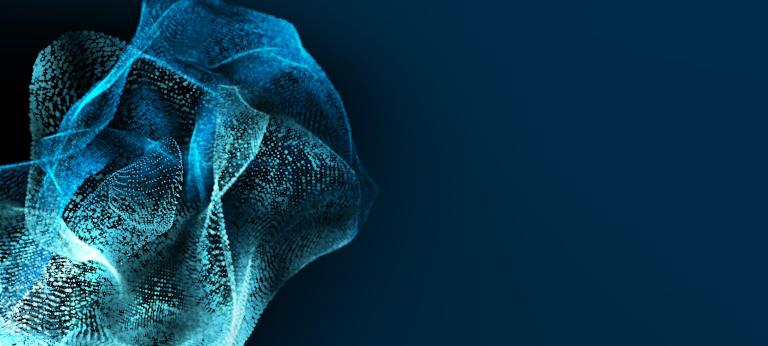

Zukunftsmarkt Batterie-Recycling: Verpasst Europa (wieder) den Anschluss?
Hersteller und OEMs brauchen verlässliche Rahmenbedingungen – auf europäischer und nationaler Ebene
Nach Startschwierigkeiten nimmt die Mobilitätswende Fahrt auf. Allein in Deutschland, so der aktuelle Plan der Bundesregierung, sollen bis 2022 eine Million Elektroautos unterwegs sein. Weltweit wird der Anteil bis 2030 bei rund 20 Prozent batteriebetriebenen Elektro-Fahrzeugen und Plug-in-Hybriden liegen.
Damit wird auch der Bedarf an Lithium, Kobalt, Nickel und Mangan, den wichtigsten Rohstoffen für die Herstellung von Batteriezellen, weiter steigen. Vor allem die Nachfrage nach großformatigen Lithium-Ionen-Batterien (LiB) wird bis 2025 auf rund 1.000 GWh zunehmen und sich bis 2030 mindestens nochmals verdoppeln. Das lässt jährliche Wachstumsraten von 35 Prozent bei Lithium beziehungsweise mehr als 50 Prozent bei Nickel erwarten.
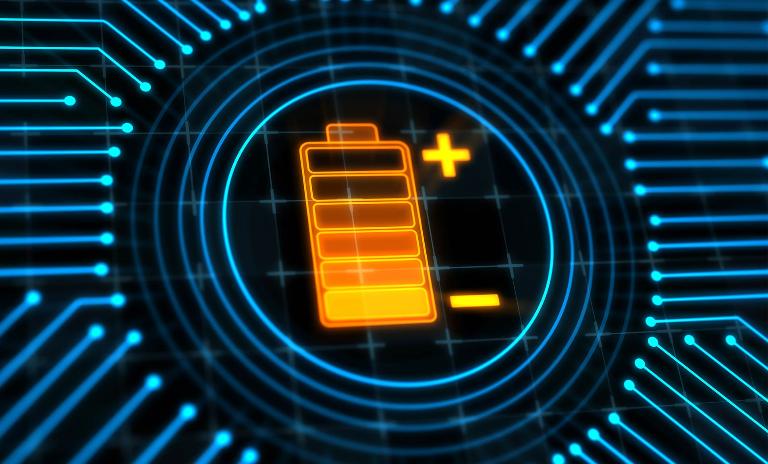
Künftige Versorgungsengpässe sind dank neuer Förder- und Raffineriekapazitäten zwar unwahrscheinlich. Trotzdem müssen die anhaltenden Preisrisiken aufgrund der hohen Branchenkonzentration im Bereich Rohstoffe und Raffinerieprodukte ebenso abgefedert werden wie politische Risiken in den wichtigsten Abbauländern in Afrika, Asien und Südamerika, wie der Ende Oktober von Indonesien angekündigte Export-Bann für Nickelerz zeigt.
Recycling: Wichtige Alternative zur primären Rohstoffgewinnung
Damit gewinnt das Thema Recycling neue Bedeutung. Denn in der Wiederverwertung alter Elektro-Akkus schlummert ein großes, bislang kaum genutztes Potenzial. Auch die Gesetzgeber machen Druck: Geht es nach dem Willen der EU-Kommission, deren neue Recycling-Richtlinie bis 2024 in nationales Recht umgesetzt werden soll, muss künftig ein deutlich größerer Materialanteil als bisher recycelt werden. Dazu sollen Auto- und Batteriehersteller ein flächendeckendes Sammel- und Wiederverwertungssystem aufbauen. Rund die Hälfte des Gewichts von Lithium-Ionen-Batterien (LiB) soll künftig wiederverwertet werden.
Im industriellen Recycling dominieren dabei im Moment vor allem zwei Verfahren: einmal das pyrometallurgische, bei dem Nickel, Kobalt und Kupfer in einem Schmelzverfahren zurückgewonnen werden. Alternativ werden hydrometallurgische Verfahren eingesetzt, bei denen der metallische Bestandteil und die recycelten Metalllösungen durch Auslaugen gelöst werden.
Zwar verfügt die EU für 2020 über ausreichende Kapazitäten für das polymetallurgische Recycling. Gemessen an dem in der EU-Batterierichtlinie festgeschriebenen Ziel für das wiedergewonnene Material hat das Verfahren jedoch seine Grenzen – so lassen sich Lithium und Mangan nicht effizient zurückgewinnen – und ist daher nicht besonders wirtschaftlich. Anders sieht es bei hydrometallurgischen Konzepten aus, die ein zirkuläres Wiederverwertungssystem erstmals in greifbare Nähe rücken lassen. Im Rahmen von Pilotprojekten unter optimalen Bedingungen wurden damit bereits hohe Rückgewinnungsquoten erzielt.
"Mit dem Hochlaufen dieser Antriebsform wird das Recycling von E-Autobatterien immer attraktiver. Wenn Europa hier nicht einmal mehr den Anschluss verlieren soll, muss die Politik jetzt mit klaren Rahmenbedingungen für ein funktionierendes Kreislaufsystem sorgen."
Recycling: Absicherung gegen schwankende Rohstoffpreise
Der ökonomische Nutzen der genannten Recycling-Verfahren ist also vielversprechend. So ist, je nach Zusammensetzung der Zelle der potenzielle Nettogewinn aus dem Recycling eines mittelgroßen Akkus bei 12 Euro bis 15 Euro je kWh bzw. 600 Euro bis 1200 Euro anzusetzen (vgl. Abb. am Beispiel eines mittelgroßen Packs mit neuester Zellchemie NCM811). Ausgehend von einer Recycling-Rate von 80 Prozent nach zehnjähriger Nutzung könnte sich der "Profit-Pool" des Recycling-Markts (basierend auf den Kosten für die mechanische Behandlung und hydrometallurgische Verfahren) 2030 nach unseren Berechnungen auf 0,7 Mrd. Euro bis 1,4 Mrd. Euro bzw. 2040 auf 2,4 Mrd. Euro bis 4,8 Mrd. Euro belaufen. Bei einem Volumen von 1,7 Mio. Tonnen recycelter Batterien im Jahr 2030 könnten außerdem 250 Tsd. Tonnen Aktivmaterial (Nickel, Kobalt, Mangan, Lithium) zurückgewonnen werden. Das entspricht rund 20 bis 30 Prozent des Kobalt- und Nickel -Bedarfs in der EU.
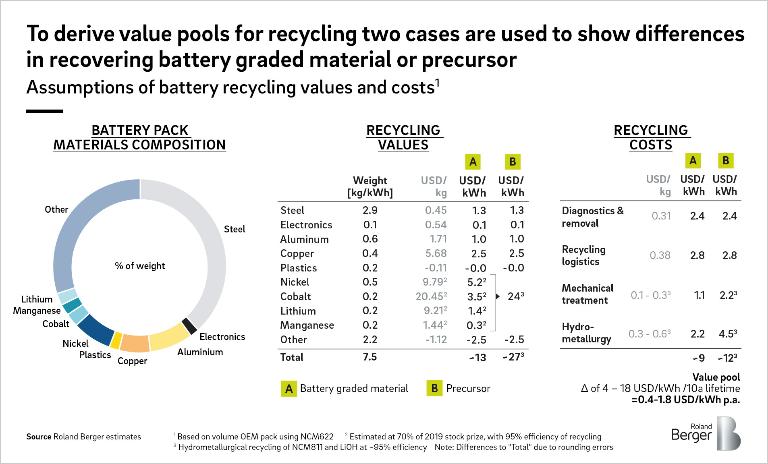
Technologie und Kapazitäten konzentrieren sich in China
Kein Wunder, dass der Markt derzeit stark in Bewegung ist. Immer mehr traditionelle Recycling-Firmen, Zellhersteller und Hersteller von Kathodenmaterial wollen in den kommenden Jahren vom Wachstum profitieren. Derzeit betragen die Kapazitäten für LiB-Recycling weniger als 100.000 Tonnen weltweit. Dabei belegt China klar die Pole-Position: Mit 67 Prozent der globalen Produktion (in GWh Output) ist es nicht nur führend in der Zellherstellung sowie in der Herstellung von Kathoden- und Anodenmaterialien und in der Aufbereitung der notwendigen Vormaterialien. Auch im weltweiten Ranking für das Recycling von Zellen, Kathoden- und Anodenmaterialien rangiert es auf Platz 1.
Vorteil der chinesischen Anbieter: Sie profitieren von einem bereits großen Markt, werden staatlich gefördert und haben guten Zugriff auf recyclingfähiges Material. So müssen die Hersteller von E-Fahrzeugen Recyclinganlagen für Batterien einrichten und standardisieren. Diese Einrichtungen werden von Herstellern, Batterieherstellern, Schrottplätzen, integrierten Unternehmen und anderen gemeinsam genutzt. Die vom chinesischen Ministerium für Industrie und Informationstechnologie (MIIT) erst Anfang November veröffentlichten Leitlinien beschreiben dabei zwei Arten von Recyclinganlagen, die die Industrie je nach Bedarf einrichten muss: kleinere Recyclingzentren dienen vor allem der Zwischenlagerung und sind auf insgesamt 5 Tonnen Batterien beschränkt, größere, "konzentrierte Lagerstätten" haben eine Mindestkapazität von 30 Tonnen und sind für die Langzeitlagerung ausgelegt. Von den Betreibern der Anlagen wird übrigens auch erwartet, dass sie digitale Technologien nutzen, um Daten über ihr Inventar zu verfolgen, zu sammeln und an die Hersteller weiterzugeben. Diese müssen die Recycling-Daten wiederum "zeitnah" melden. Bestehende Anlagen haben sechs Monate Zeit, die Anforderungen der Richtlinien zu erfüllen.
Mit mindestens vier „Gigafactories“, die in Deutschland, Polen, Schweden und Ungarn geplant oder bereits im Aufbau sind, eröffnet der Recycling-Boom auch für die europäische Industrie gute Chancen auf eine marktführende Position.
Dazu benötigt sie allerdings klare Rahmenbedingungen von der Politik: Neben der Förderung von Grundlagenforschung, die vor allem im Bereich der Wiederaufbereitung von Aktivmaterialien über den in Asien bereits angewandten Stand der Technik hinausgehen muss, sollten Standards gesetzt werden, z. B. für maschinenlesbare Informationen auf Akkus, um so die Automatisierung der Demontage und die rasche Industrialisierung von Recyclingverfahren voranzutreiben. "Track&Trace"-Mechanismen, wie sie in China heute bereits Standard sind, sollten verpflichtend und einheitlich für Europa eingeführt werden und zur Absicherung des Rohmaterialzugriffs und Entwicklung der Industrie in Europa sollten Exportbeschränkungen für Alt-Zellen und zu recycelnde Aktivmaterialien in Erwägung gezogen werden. Damit die Unternehmen Planungssicherheit haben, sollte außerdem die Umsetzung der neuen EU-Batterierichtlinie in nationales Recht massiv beschleunigt und der Gestaltungsspielraum soweit irgend mölglich beschränkt werden. Es gilt, jetzt die notwendigen Kapazitäten aufzubauen – bevor asiatische Wettbewerber auch dieses Feld unter sich aufteilen.