Unsere Beratungsleistungen bieten Ihnen eine Reihe von zukunftsorientierten Lösungen, die Ihr Unternehmen bei der Transformation Ihrer Fertigungsansätze in Richtung Next Generation Manufacturing unterstützen.
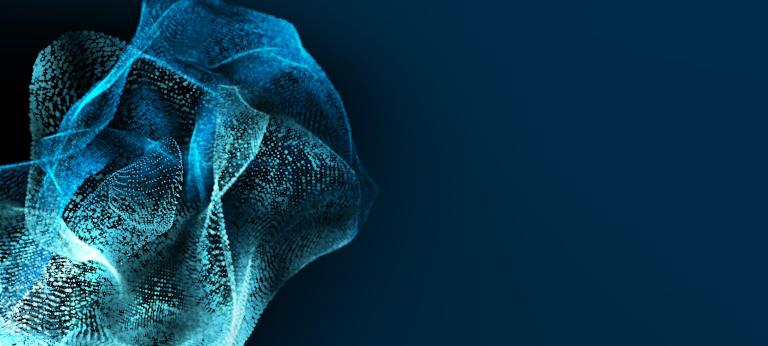
_download_preview.jpg)
Was wurde aus der Industrie 4.0?
Von Bernhard Langefeld und Michael W. Rüger
Wie Automotive-Unternehmen bei der digitalen Fertigung vorangehen – und was andere Industrien daraus lernen können
Das Konzept der Industrie 4.0 wurde in Deutschland vor mehr als einem Jahrzehnt geprägt und bezeichnet das enorme Fortschrittsversprechen einer umfassend digitalisierten Fertigung. Seit damals ist viel Zeit vergangen, und in vielerlei Hinsicht hat sich die Automobilindustrie an die Spitze der Entwicklung gesetzt. Um (überzogene) Erwartungen von (tatsächlicher) Realität zu trennen, führte Roland Berger kürzlich eine ausführliche Befragung unter internationalen OEMs, Tier-1-Zulieferern und anderen Kennern der Automotive-Branche durch. Der vorliegende Artikel fasst die wichtigsten Ergebnisse des ausführlichen Roland Berger Berichts zusammen und dokumentiert Erkenntnisse aus der Geschichte der Industrie 4.0, von denen auch andere Sektoren profitieren können.
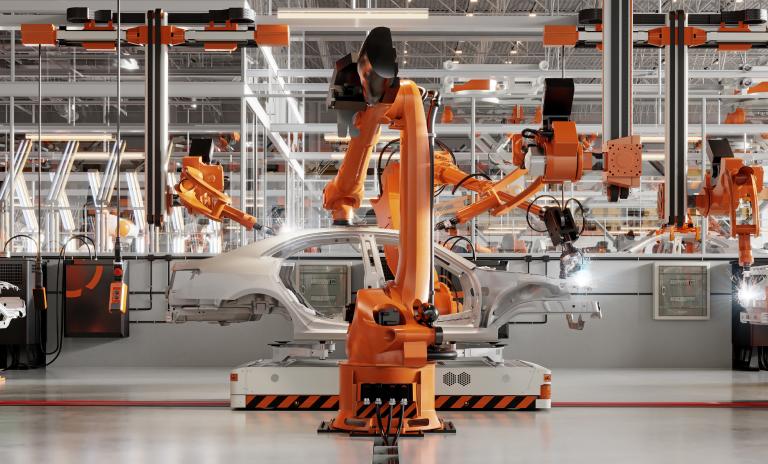
"Da sich verschiedene Prozesse und/oder Technologien in der Automobilherstellung unterschiedlich gut für eine Digitalisierung eignen, ist es überaus wichtig, für jeden einzelnen Anwendungsfall genau abzuwägen, wie viel Mehrwert durch die Digitalisierung entsteht."
Ein Jahrzehnt der digitalisierten Fertigung
Vor gut zehn Jahren begann insbesondere die (deutsche) Automobilindustrie damit, in großem Maßstab in die Identifizierung, Entwicklung und Einführung von Anwendungsfällen für die digitale Fertigung zu investieren. Mit dem Abflauen der ersten Euphoriewelle traten zahlreiche technologische und organisatorische Herausforderung zutage, von heterogenen Legacy-Infrastrukturen, über Probleme bei der Quantifizierung des Nutzens digitaler Anwendungsfälle (und entsprechenden Problemen bei der Gewinnung von Investoren) bis hin zur Notwendigkeit, die vorhandene Belegschaft neu zu schulen oder geeignete Mitarbeiter zu finden und einzustellen. Auch eine innerbetriebliche Silo-Mentalität stand der nunmehr notwendigen funktionsübergreifenden Zusammenarbeit oft im Wege.
Mehr als eine Dekade später liegt die ursprüngliche Vision einer autonomen, hochflexiblen und selbstorganisierenden Fabrik noch immer in weiter Ferne. Um herauszufinden, an welchem Punkt die Industrie 4.0 tatsächlich steht, tauchte Roland Berger tief in die Materie ein. Dabei untersuchten unsere Experten, welche Anwendungsfälle im Fokus der Automotive-Unternehmen standen, wie weit diese fortgeschritten sind, welche Unterschiede es zwischen OEMs, OESs und verschiedenen Regionen gibt und wie diese Anwendungsfälle – parallel zu den notwendigen organisatorischen Veränderungen – in der Praxis weiterentwickelt und umgesetzt werden.
Wo gibt es die Industrie 4.0 in der Automobilbranche?
Nachdem Roland Berger zunächst sieben archetypische Anwendungsfälle in der Automobilindustrie identifiziert hatte, kristallisierten sich fünf konkrete Use Cases heraus, die von der Branche bis dato priorisiert werden. Alle fünf sind Unterkategorien der sieben archetypischen Anwendungsfälle. Sie lauten: Echtzeitoptimierung von Maschinenparametern, Zustandsüberwachung und prädiktive Wartung, automatisierte Qualitätsprüfung auf Basis von visuellen/Prozessdaten, autonomer Materialtransport in der Intralogistik sowie Transportverfolgung entlang der Lieferkette.
"Für Cobots gibt es nur wenige Anwendungsfälle. Sie eignen sich meist nur für die Postautomation von Arbeitsplätzen, an denen ursprünglich manuelle Tätigkeiten verrichtet wurden."
Dass Cobots in dieser Liste nicht auftauchen, spricht für sich: Nach dem ersten Hype stellte sich schnell heraus, dass es für Cobots nur eine begrenzte Zahl von Anwendungsfällen mit einem positiven Business Case gibt. Heutzutage werden Cobots meist für die Postautomation von Arbeitsplätzen eingesetzt, an denen ursprünglich manuelle Tätigkeiten verrichtet wurden.
Da sich verschiedene Prozesse und/oder Technologien in der Automobilherstellung unterschiedlich gut für eine Digitalisierung eignen (was im Übrigen auch für andere Branchen gilt), ist es überaus wichtig, für jeden einzelnen Anwendungsfall genau abzuwägen, wie viel Mehrwert durch die Digitalisierung entsteht. Roland Berger tauchte daher tief in die Fertigungsprozesse von OEMs und OESs ein und erkundete, wie sich zum Beispiel Unterschiede zwischen Niedrig- und Hochkostenländern auf die digitalen Prioritäten der Unternehmen auswirken. Die fünf priorisierten Anwendungsfälle der Automotive-Branche machen deutlich, wo Chancen, aber auch Risiken liegen. Die folgenden Abschnitte geben einen kurzen Überblick; ausführliche Informationen finden Sie im vollständigen Bericht:
- Zustandsüberwachung und prädiktive Wartung
Trotz ihres Potenzials für mehr Verfügbarkeit und bessere Overall Equipment Effectiveness (OEE) steht die prädiktive Wartung in der Realität vor einer Reihe von Herausforderungen, seien es hohe Nachrüstkosten oder feste Wartungspläne, an die Automotive-Unternehmen gebunden sind. Aus diesem Grund finden sich in der derzeitigen Praxis nur vergleichsweise simple prädiktive Wartungsanwendungen wie z. B. die Motorstromanalyse. Komplexe Anwendungsfälle, die komplette Systeme abdecken (z. B. Industrieroboter), befinden sich noch in der Entwicklungsphase. Trotz dieser Herausforderungen ist angesichts des beträchtlichen Nutzens der prädiktiven Wartung – insbesondere für Großanlagen wie CNC-Bearbeitungsmaschinen in der Komponentenfertigung oder Industrieroboter im Karosseriebau – und der investierten Ressourcen davon auszugehen, dass die Zahl der Anwendungsfälle in den kommenden Jahren drastisch steigen wird. - Automatisierte Qualitätsprüfung
Durch die Feststellung etwaiger Anomalien in Prozess- und Sensordaten lassen sich potenzielle Qualitätsprobleme zuverlässig detektieren und prognostizieren. Prozess- und Sensordaten können außerdem dazu dienen, Stichprobenkontrollen durch datenbasierte Prüfungen zu ersetzen und zusätzliche, frühzeitigere sowie präzisere Qualitätschecks durchzuführen. Dabei wird grundsätzlich zwischen einer visuellen Prüfung und einer Prüfung auf Basis von Prozessdaten unterschieden.
Qualitätsprüfung auf Basis von visuellen Daten: Hier liegt der Schwerpunkt auf visuellen Verfahren für die Prüfung einzelner Bauteile, die Inline-Prüfung und die frühe Prüfung. Im Zuge des Deep Machine Learning wurden bedeutsame Verbesserungen erzielt, sodass die visuelle Qualitätsprüfung beträchtlichen Mehrwert bietet. Grundsätzlich ist die Technologie weit genug ausgereift, um schnell implementiert zu werden. Allerdings befinden sich die meisten Anwendungsfälle noch in einer Früh-/Pilotphase bzw. in der Entwicklung. In den kommenden Jahren dürfte die Kombination aus kostengünstigen Kameras und komplexen ML-Modellen jedoch zu umfangreicheren Rollouts führen.
Qualitätsprüfung auf Basis von Prozessdaten: Auch hier lassen sich einfache Anwendungen wie die Qualitätskontrolle von geschraubten Teilen am besten implementieren, da viele Modelle und Prozesssteuerungen bereits an Ort und Stelle sind. Werden bekannte Prozesse und Parameter mit einfachen Statistikmodellen kombiniert, kann dies messbaren Nutzen haben. Insgesamt ist der Ansatz jedoch noch nicht so weit ausgereift, wie dies bei visuellen Verfahren der Fall ist. Komplexere Anwendungsvarianten werden erst noch erforscht. - Echtzeitoptimierung von Maschinenparametern
Experten für industrielle Prozesse und die Definition von Maschinenparametern sind selten und teuer. Umso verlockender ist es, sie durch automatisierte Lösungen zu ersetzen, wie sie beispielsweise bei der Optimierung von Prozessparametern für das Reinraummanagement schon heute zum Einsatz kommen. In der Praxis finden sich bereits erste Anwendungsfälle. Diese sind jedoch noch sehr rudimentär und basieren ebenfalls auf ausgewählten Parametern für vollständig beherrschte Prozessabläufe. Die Fülle an Schwierigkeiten dürfte auch hier dazu führen, dass in den kommenden zehn Jahren kaum komplexere Anwendungen hinzukommen werden. Bis auf weiteres wird sich die Optimierung von Maschinenparametern in der Automotive-Industrie daher auf die Einspeisung von Informationen beschränken, die als Entscheidungshilfe für menschliche Prozessexperten dienen. - Autonomer Materialtransport in der Intralogistik
Durch sein substanzielles Sparpotenzial steht dieser Anwendungsbereich ganz oben auf der Prioritätenliste der Automobilunternehmen. Die Automatisierung des indirekten Materialtransports (ergänzend zu direkten, weitgehend automatisierten Transportaufgaben) könnte die Arbeitskosten und Fehler-/Ausschussraten in Produktionsumgebungen erheblich reduzieren. Da Herausforderungen wie variierende Objektformen und Arbeitsbereiche, in denen sich auch Menschen aufhalten, noch nicht abschließend gelöst wurden, sind dem autonomen Transport großer und schwerer Gegenstände derzeit noch Grenzen gesetzt. Sehr gut funktioniert hingegen der Transport von kleinen, leichten und weniger kritischen Komponente durch fahrerlose Transportfahrzeuge (AGV), sowohl zwischen Warenlagern und Fertigungsstraßen als auch in der Distributionslogistik. - Transportverfolgung entlang der Lieferkette
Nachdem sie sich anfänglich auf die Eingangslogistik für kritische Komponenten konzentriert hatten, gehen einige OEMs nun dazu über, die Auslieferung von fertig montierten Fahrzeugen zu verfolgen. Das automatisierte Echtzeit-Tracking kann gerade dann erhebliche Vorteile haben, wenn Produktionsausfälle sehr hohe Kosten verursachen – entsprechend attraktiv es für viele Automotive-Player.
Inwiefern wirkt die Automobilindustrie als Entwicklungs- und Umsetzungstreiber?
Roland Berger befragte führende Branchenvertreter und Experten danach, wie sie mit den oben erwähnten Herausforderungen und Schwierigkeiten umgehen. Der zugehörige Bericht zeigt auf, dass es in zwei Schlüsselbereichen vergleichbare Muster und Blaupausen gibt: bei den Organisationsstrukturen und Betriebsmodellen sowie bei der IT/OT-Architektur.
- Organisationsstrukturen und Betriebsmodelle
Zur Überwindung der Redundanzen und Diskrepanzen, die traditionell unabhängige Produktionsstätten mit sich bringen, bevorzugen insbesondere größere, digitalisierungsaffine OEMs Organisationsstrukturen nach dem Hub-and-Spoke-Prinzip. Unter Verwendung eines weitgehend an Use Cases orientierten Ansatzes bündeln zentrale Einheiten dabei die notwendigen digitalen bzw. Produktionskompetenzen und kooperieren eng mit (dezentralen) Produktionsstätten. Die meisten Unternehmen setzen auf ein fünfstufiges Modell, um vielversprechende Anwendungsfälle zu identifizieren und zu priorisieren, Prototypen zu entwickeln, zu testen und sie anschließend im gesamten Produktionsnetzwerk auszurollen. Der vollständige Roland Berger Bericht schildert ausführlich, wie „Nabe“ (Hub) und „Speichen“ (Spokes) kommunizieren und zusammenwirken müssen, damit dieses Modell effizient funktioniert.
- IT/OT-Architektur
Mit einer übergeordneten IT/OT-Architektur können Automotive-Unternehmen die Redundanzen und Abstimmungsfehler vermeiden, die häufig auftreten, wenn Use Cases ohne Zusammenhang aneinandergereiht werden. Eine übergeordnete IT/OT-Architektur hat den Vorteil, dass sie von vornherein standardisiert und interoperabel ist und ein zügiges, effizientes und kohärentes Rollout neuer Anwendungsfälle ermöglicht. Führende deutsche OEMs arbeiten bereits an der Einbindung von Tier-1-Zulieferern in die entsprechenden Architekturen, während sich OESs derzeit stärker auf die interne Harmonisierung konzentrieren.
Was können andere Branchen von der Automobilindustrie lernen?
Die Pionierarbeit, die Automotive-Player im Bereich der digitalen Fertigung geleistet haben und weiter leisten, birgt wertvolle Erkenntnisse, von denen zahlreiche andere Branchen profitieren können. Der detaillierte Roland Berger Bericht destilliert daraus vier praxisrelevante Empfehlungen für Unternehmen, die die Errungenschaften der Industrie 4.0 auf ihren Sektor übertragen wollen:
- Priorisierung von Anwendungsfällen und Ressourcen
Durch die Quantifizierung des Mehrwerts von Kostenersparnissen, Qualitätszuwächsen, Energieeinsparungen usw. können Unternehmen gezielt diejenigen Anwendungsfälle identifizieren und umsetzen, die den größten Gewinn versprechen. Das Resultat ist ein überzeugender Business Case, der eng an das ökonomische Umfeld und die regionalen Voraussetzungen gekoppelt ist. - Schaffung einer Hub-and-Spoke-Struktur
In einer solchen Organisationsstruktur verfügt eine zentrale Einheit (Hub) sowohl über Datenanalyse- und andere produktions-/IT-bezogene Fähigkeiten als auch über die Autorität, Veränderungen in dezentralen Produktionsstätten (Spokes) zu veranlassen. Letztere wiederum müssen die Maßnahmen der zentralen Einheit uneingeschränkt unterstützen, weshalb Transparenz und eine überzeugende, wechselseitige Kommunikation unverzichtbar sind. Der durch die digitale Fertigungseinheit erzielte Mehrwert muss für alle klar erkennbar sein. - Umbau von Schulung und Talentgewinnung
Vorhandene Schulungs- und Rekrutierungsmodelle müssen angepasst werden, um der wachsenden Bedeutung von Digitalisierungs- und Datenanalysekompetenzen Rechnung zu tragen, den Umgang mit Automatisierungstechnik zu vermitteln und regionale Führungskräfte und Standorte von den Vorteilen der digitalen Fertigung zu überzeugen. - Definition von IT/OT-Ziel und Roadmap
Sobald Ergebnisse aus ersten Anwendungsfällen vorliegen, muss ein IT/OT-Ziel definiert und eine entsprechende Roadmap abgesteckt werden. Nur so lässt sich das ganze Potenzial der digitalen Fertigung ausschöpfen, ohne dass es langfristig zu wertmindernden Überlappungen und Redundanzen kommt.
Ausführliche Informationen zu diesem Thema sowie praxisbezogene Tipps und Beispiele finden Sie im vollständigen Roland Berger Bericht. Bei Fragen, Anmerkungen und Vorschlägen können Sie sich jederzeit per E-Mail an uns wenden. Wir schätzen Ihren Input und freuen uns darauf, von Ihnen zu hören.
Register now to download the full study on “Whatever happened to Industry 4.0” including key insights, an outlook on the developments of the automotive industry as well as use cases for respective players within the industry. Additionally, you'll get regular insights into automotive topics.