Resilience is a new paradigm for China – It is calling for adaption of business model, operating model, management and decision-making systems
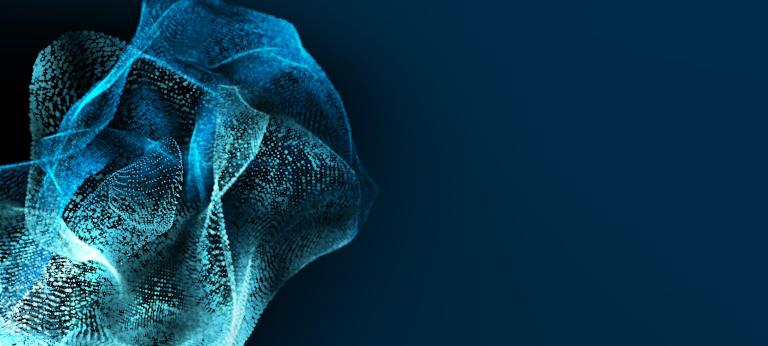

Engineering Excellence: The hidden driver of automotive profitability
The global automotive industry is shifting gears—fast. After decades of expansion driven by globalization, electrification, and software innovation, the rules of the game are shifting. Volume growth has slowed. Margins are tightening. New technologies are arriving late and over budget. The pressure on costs is intensifying by the quarter.
For OEMs and suppliers, this new reality calls for a hard reset—on cost, yes, but also on how organizations plan, develop, and launch the next generation of vehicles and modules.
This is a challenge of engineering performance, and the companies that crack it will pull ahead and drive innovation and profitability in a fiercely competitive market.
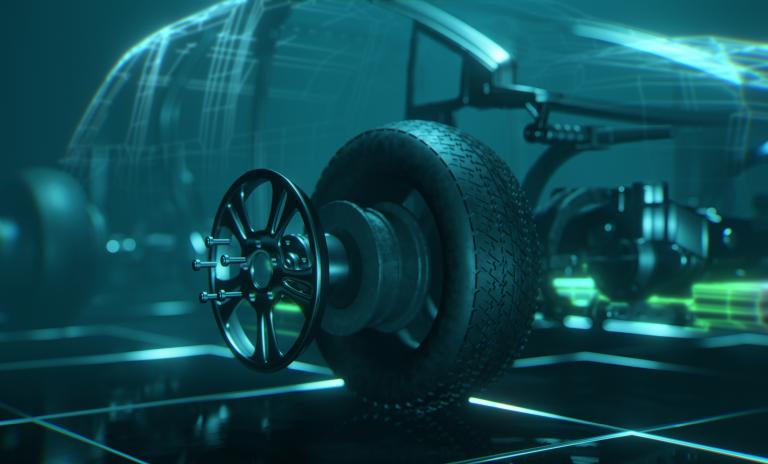
Growth has stalled. Complexity has not.
Start with the fundamentals: global light vehicle sales are no longer rising at the same pace. After COVID disruptions, supply chain chaos, and inflation shocks, the market has entered a phase of slower, more volatile growth, but at the same time competition has significantly intensified.
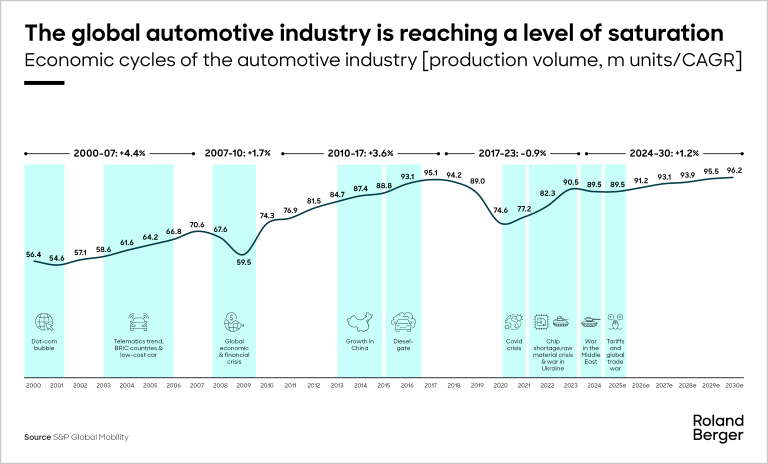
"Engineering excellence isn’t a cost-cutting lever — it’s a strategic advantage. The companies that master it will unlock both profitability and resilience in a changing automotive landscape."
The transition to electrification, once expected to supercharge the sector, has been more uneven than hoped. BEV sales continue to rise, albeit at a slower rate than initially forecasted. Consumers remain cautious. Charging infrastructure lags behind. And regulatory signals are still mixed.
Meanwhile, for Western OEMs, the race to develop software-defined vehicles (SDVs) has hit a wall. Nearly every major OEM that launched bold SDV programs five years ago is now facing delays of two to three years. Costs are higher, complexity is deeper, and legacy platforms aren’t cooperating. Chinese OEMs, on the other hand, are increasingly outpacing Western OEMs in this area, creating added competition driven by a combination of structural advantages, market dynamics, and strategic focus. While some Western OEMs are investing heavily to catch up, the execution remains uneven. By contrast, China’s new generation of OEMs were "born digital", giving them a multi-year head start.
Margin pressure is getting personal
It’s not just top-line pressures—profitability is eroding across the board. OEM EBIT margins are slipping. Supplier margins have fallen more than 2 percentage points since 2017. And rising R&D costs are squeezing budgets even further.
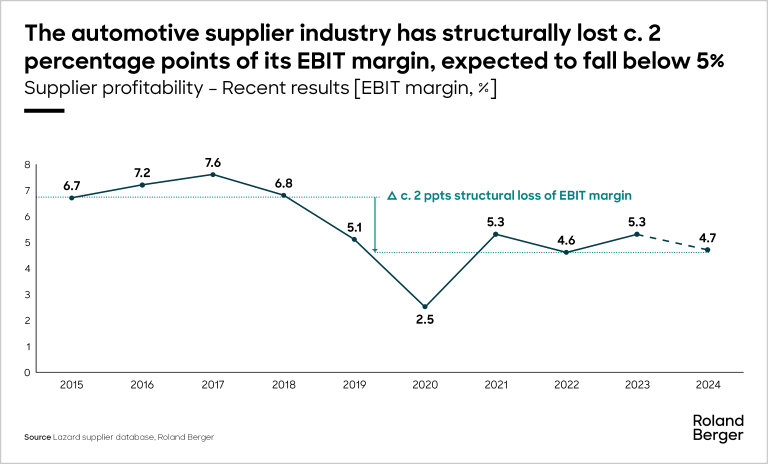
"To stay ahead, OEMs must rethink how they develop products—not just to cut costs, but to unlock speed, quality, and innovation at scale."
Automakers are fighting back with either conventional performance improvement programs or with radical approaches tackling structural disadvantages, as seen with the AUDI brand in China. Tesla aims to halve unit costs for its next-generation vehicles. General Motors, Toyota, and Volkswagen are pursuing multibillion-dollar savings goals. But hitting these targets won’t come from shaving procurement costs, trimming budgets, and axing unprofitable offerings alone.
Hidden costs, visible gains
Let’s be honest: many organizations have been leaving money on the table. Our teardown benchmarks across various systems such as EV platforms, drivetrains, and infotainment modules consistently reveal 10–40% cost differences for comparable components.
In one teardown, we found a $440 per-unit cost gap between a Western and a Chinese electric drive unit, with no meaningful difference in power, torque, or size.
These aren’t just sourcing inefficiencies. They stem from legacy complexity, unclear engineering priorities, and fragmented collaboration across the product creation lifecycle. In other words: they’re fixable.
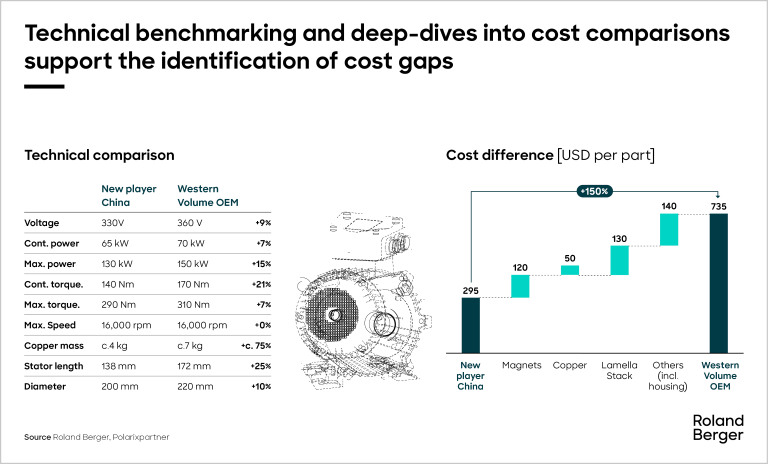
The race is on—and China is pulling ahead
Many Chinese OEMs are already proving what streamlined engineering can deliver. In benchmarking studies, they show up to a 14-month advantage in end-to-end product development process.
They achieve this through:
- Clearer platform strategies and architectures
- Earlier supplier integration and leveraging off-the-shelf solutions
- Digital-first development and validation
- Leaner decision-making
This isn’t about cutting corners. It’s about eliminating friction, so that every engineering decision moves the product forward instead of adding layers of delay and cost.
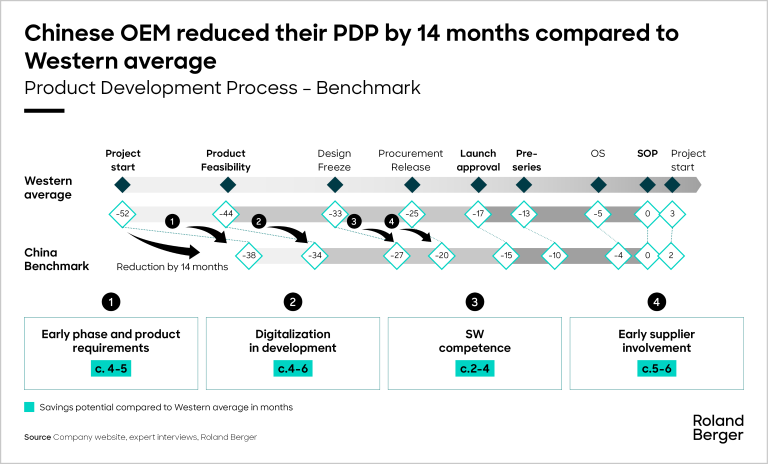
"It’s not just about trimming costs. Engineering excellence is about smarter decisions, faster development, and delivering real value to customers and the bottom line."
Where leading companies are investing now
1. Simplifying complexity
SKU proliferation drives up cost, confuses operations, and slows time to market. The best players are taking a scalpel to the portfolio. One client reduced its SKUs by 45% and saw a significant EBITDA improvement.
Just as important, leading companies are re-evaluating how products are specified in the first place—challenging over-specification, aligning engineering targets with real customer value, and streamlining requirements across platforms. When specification discipline improves, so does cost performance—without compromising quality or market relevance.
2. Digitizing the engineering workflow
Digitally integrated engineering environments—powered by cohesive PLM functionalities, simulation platforms, and now, generative AI—are transforming development timelines and outcomes.
3. Resetting the talent and capability base
The future of engineering requires new skills, including AI and software, systems integration, cybersecurity, and cost-centric design. CTOs must rethink not just hiring, but how teams are organized to deliver impact.
From fragmented cost cuts to strategic rewiring
The stakes have never been higher. Capital is more expensive. The industry is at a turning point. And the pressure to deliver smarter, faster, and leaner has shifted from a boardroom topic to a survival strategy.
Here’s the good news: cost performance doesn’t have to come at the expense of innovation. In fact, the opposite is true. Engineering Excellence is the path to both.
The untapped potential lies in engineering.
How products are specified, developed, validated, and delivered—this is where the real leverage lies.
At Roland Berger, we believe cost performance and engineering performance are inextricably linked. And yet, too often, product development decisions are made in silos, disconnected from what the market truly values or what customers are willing to pay for. The result? Overengineered solutions, missed cost targets, and significant differences in bill-of-material (BOM) costs for comparable products.
We work with clients to bridge that gap, building what we call Engineering Excellence: a holistic framework that touches every aspect of the broader development process.
It includes:
- A clear engineering strategy aligned with product and platform vision, as well as overall business goals and objectives
- Agile development and project management models that deliver in less time and with fewer resources
- Organizational enablers—from skills and talent to tools and culture
When done right, it doesn’t just reduce cost. It increases speed, boosts product quality, and makes the organization far more resilient.
For senior leaders, the imperative is clear: elevate engineering to a board-level agenda, drive transparency across the development process, and focus relentlessly on value—not just features. Capturing the full value of engineering transformation demands more than operational fixes—it requires strategic alignment from the top.
Roland Berger would like to thank Jan Schulte for his contribution to this article. Jan Schulte is the Managing Director North America for Polarixpartner , a Roland Berger company.