

How to thrive in the 2020s: Five engineering challenges for COOs
More efficiency from a functional focus, automation and modularization
Almost every industry will be familiar with the problem: Technology trends, regulatory trends and market trends conspire to make product development increasingly complex – and increasingly expensive. Profit margins in the automotive industry have come under pressure recently as a result, but other sectors are also struggling. Companies are exceeding their R&D budgets ever more frequently, and five key factors are mainly to blame.
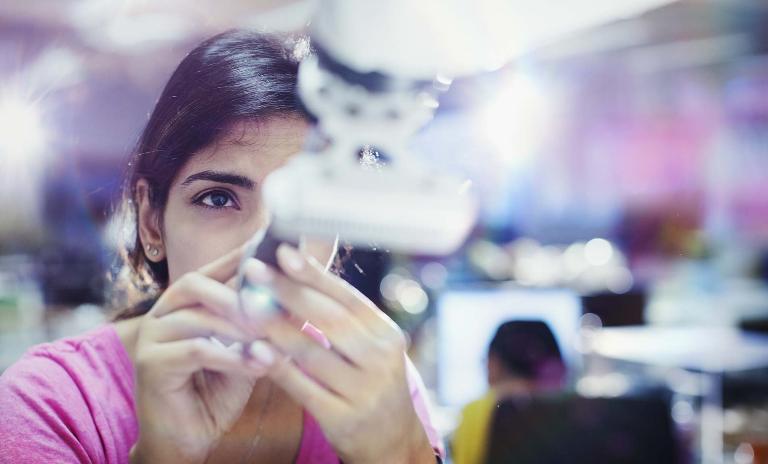
"The competitive R&D of the future will meet three conditions: It will be aligned to functions, engineer products with short time-to-market and the most efficient number of variants, and have a mastery of system complexity."
1. The requirement to maintain dual-track capabilities:
New technologies need to be developed and old ones sustained in parallel
What's happening in the automotive sector right now provides the most striking example of this. While the industry had long assumed that electric drives would sooner or later replace the internal combustion engine, it is now certain that both technologies will have to be maintained and developed in parallel for at least the next 20 years. The result? Additional personnel needs in R&D, growing portfolio and system complexity, and rising application costs.
But it's not just the automotive OEMs that are suffering. The switch from "conventional" technologies such as hydraulics and pneumatics to electrical, electronic and digital technologies is keeping the captains of many industries up at night. The fact that different tech concepts are all being applied simultaneously makes the situation even harder to master. And it drives up costs, especially in research and development. Even in the railway industry, a parallel technology has become established in the form of the "compressed-air-free train" and suppliers will need to adapt their own technology to that. In other words, they'll have to advance the development of their electromechanical brakes to such a point that even the necessary redundant systems do not use compressed air. Last but not least, the technology also has to be aligned with the law due to the high safety requirements in the industry.
Questions remain, however, over whether the compressed-air-free train will establish itself as the leading technology globally on a medium-term horizon. Even if it does, it will still take decades – not least because of the very long train lifecycles. Rail suppliers are thus faced with the challenge of operating compressed-air-free and conventional braking systems in parallel. For both, they need qualified employees, advanced development projects, capacities for prototypes and testing, as well as special process technologies.
2. The end of the mechanical age:
Integration of mechanics, electrics, electronics and software
Electrification, autonomous capability and connectivity – through the growing proliferation of IoT devices, for example – are important prerequisites for product success. Functionality now plays a far greater role than the physical components of a given product. In this context, system integration is a pain point within R&D as it's a cause of rapidly rising costs. The growing autonomy of machines and vehicles, for example, requires flawless interaction between a wide range of components within the system, such as sensors where steering, brakes and axles all interact. Thinking on a component-by-component basis is therefore no longer effective.
Moreover, changes in user behavior and expectations often lead to traditional mechanics being replaced by other technologies. The most convenient way to open a lock may be an app instead of a key, for example. For this to work, however, the mechanics of the lock must be combined with electrics, electronics and software. The integration of software in mechanical components is also a commercial consideration. Nowadays, trains and cars are no longer slowed down by mechanical or pneumatic systems alone, but by software-supported algorithms in order to reduce wear and tear and keep the total cost of ownership down.
What we are seeing, therefore, is (mechanical) components turning into more and more (mechatronic) systems. So, suppliers with a mechanical focus not only face the task of building up new competencies in electrics, electronics and software, disciplines which are fairly new to them, but they also have to rethink their entire product development process and the product architecture behind it.
3. Red tape in R&D:
Rising documentation needs tie up resource capacity
Documentation is becoming increasingly important throughout the entire product development process. Not only are companies having to test the functionality and quality of a product, but the creation of the product itself necessitates ever stronger regulatory monitoring. In times of increasing autonomy, this serves above all else to legally ensure the product's functional safety. Although autonomous machines and vehicles will one day make more and more decisions for the user, the manufacturer will be held responsible in the event of mechanical malfunction and any accidents that result.
Companies are subject to strict regulatory requirements in documenting the R&D process. The SPICE process standard, for example, sets special process requirements that must be fulfilled in order for certification to be granted. This causes considerable headaches for many suppliers in the automotive industry, because orders worth millions depend on "A-SPICE conformity" and the associated certification.
A decline in documentation and vehicle safety requirements within product development is unlikely any time soon – unfortunately for the companies and employees concerned. Engineers will therefore continue to be kept from their actual work – adding value in construction, design or testing – by the need to perform administrative tasks.
However, the growing admin requirements are also a significant driver of cost and effort in R&D departments throughout industry. The highly diverse tool landscape with its many interfaces keeps R&D departments very busy manually inputting, transferring and updating data. A great deal of time is also spent on creating presentation decks. The administrative effort quickly adds up to 20 to 30 percent of a developer's working time – which is why you often hear them disparagingly referred to as "PowerPoint engineers".
4. A difficult balance to strike: As customer and market demands rise, so too do application costs and the sheer number of variants
Both globalization and the recent rise in protectionism are leading to an ever-increasing number of variants across different countries, as separate regulatory requirements apply in each market. This presents a dilemma for many companies: Either they have to accept the costly development of a variant designed to meet the legal requirements in the country concerned, or they must pull out of that market completely.
Strategic discussions over limiting the number of variants and applications quickly mutate into a test of will between the corporate divisions: While R&D managers see their budgets straining at the seams and therefore urgently demand a reduction in country-specific variants, colleagues on the sales side fear dwindling sales volumes.
The problem of the product range continuing to grow in tune with the scope of global customer requirements is basically unsolvable. The gap between high-end solutions and standard products is simply too wide now. When it comes to capital goods investments, emerging markets often lack the infrastructure to have connected production machines, for example. As a result, some expensive functions cannot even be used by the customers there, making the product too costly when measured against the added value that the customer can perceive. In Western markets, on the other hand, these functions are absolutely necessary in order to maintain technology leadership. Further, it is well known that Asian end customers are extremely price sensitive. This increases the demand for cheaper standard solutions at the expense of costly high-end solutions. OEMs face the challenge of managing this broad spectrum while keeping complexity as low as possible. Many find themselves torn between the "blue ocean" of technology leadership and the "red ocean" of commoditized, cost-leading projects.
5. Product development on fast forward:
No let-up in the pressure on time-to-market
Product lifecycles are becoming ever shorter, partly as a result of the shorter lifecycles of individual components such as displays and connectivity systems. The reason for this is not so much the actual "durability" of the products as the fact that product improvements are coming onto the market faster. Consumer electronics is one big area where the useful life of products is constantly falling in the eyes of customers: On the one hand, technical innovations and improved product releases –for smartphones, say – fuel customer demand. And on the other hand, frequent changes in the interfaces such as mini-/micro-USB, USBC, etc. actually force consumers to change models because of incompatibilities. Customers expect similarly fast technological innovations in their user experience with other products around them, from cars to washing machines.
All five of the above factors have one thing in common, which is that if your organization, processes, systems and resources are not carefully designed, development costs can quickly run away with you. Because the task of developing even more of something that is beyond the competency profile you've been working on for decades is anything but trivial. And it certainly doesn't come at no cost.
Looking forward: What are the steps to Next Level Engineering?
Let us now turn our attention to possible solutions. But be warned: There are no "quick wins" when it comes to overcoming the challenges outlined above.
Future-proof structures can break open silos and foster innovation
R&D teams that concentrate on developing physical components – in all the separate component categories in automotive manufacturing, for example – are likely to be obsolete in the long term. Instead, their organizational structure must be aligned along functions and must become much less opaque. What this means is: team and project structures instead of rigid department silos – cross-departmental cooperation with efficient communication and digital workflows.
In our experience, it is crucial to create efficient informal cooperation channels that connect employees at different locations – even if they're only in the building next door. The kitchen or break room, for example, has often been the birthplace of new patents. The apparently aimless chatting between colleagues is a nucleus for the creativity and innovative power of companies that should not be underestimated. In virtual teams, "digital break rooms" can be created, which may take the form of corporate social media.
Automation of admin tasks to free up time
Few companies are so far benefiting from the possibilities offered by automating administrative activities in R&D, for example through robot process automation (RPA) and automated analysis of requirements specifications. In the medium term, however, no one will be able to afford or want to have employees spending about a quarter of their time on administrative tasks instead of developing, testing and validating products. Data entries that have to be transferred from one system to another or documented in Excel tables due to missing interfaces should be a thing of the past in the next ten years, if nothing else.
Robot process automation solutions can handle repetitive processes and tasks automatically. There is no time-consuming "training" required, they simply copy human interactions with the user interfaces of software systems quickly and easily. In doing so, they relieve users of repetitive, non-value-adding and, above all, annoying tasks and create space for the really important work to be done.
Make system complexity manageable with new expertise and a strong architecture
R&D departments in the traditional mechanical engineering industry need a better understanding of systems from their employees, and they especially need more critical expertise in electrics, electronics and software. The "war for talents" that everyone is talking about is certainly being fought here, too – partly because traditional industrial companies find it difficult to define the exact profiles of strategic competencies that they require . In many cases, therefore, they often bring in external R&D resources to help them with "firefighting". However, such a short-term orientation comes at the expense of a real strategy for creating value.
When recruiting these profiles, industrial companies must get off the beaten track and be much bolder in their approach. They may, for example, have to recruit internationally, even if the lack of language skills is initially an obstacle, or address completely new target groups. The image of German companies, known for their 35-hour weeks and 30 days' vacation allowance, is no longer a guarantee that the search for the right candidate will be easy. But even when the highly sought-after talents have successfully been brought on board, the work is not done yet. All of the different areas and functions need to be linked up – after all, it is a well-known fact that a software engineer thinks completely different to a "traditional" mechanical engineer.
This poses a particular challenge for suppliers, given that OEMs across industry verticals are indeed transitioning toward handing over the system competency in their requirements specifications to the suppliers. That will mean suppliers not only handling the systems engineering of their own components, but also having the ability to integrate them into the OEM's system as a key competitive factor.
In addition to the new requirements profiles within the workforce, product architecture is a key lever in making the complexity of systems more manageable – instead of being controlled by them. The keyword here is modularization. Although companies have been talking about this for years, in our experience engineers have not yet dared to tackle the issue consistently enough. That has its price and is evident in systems engineering, in particular, with engineered-to-order shares of up to 40% of the order volume. Clearly, with the increasing dominance of mechatronic and software-based systems, the cost and effort involved in validating systems increases exponentially with their complexity. If just one single piece is changed, a non-modular system must always be completely revalidated. It would be much more efficient to have reference validation for the individual modules.
Ensure permanent adaptability with OPERA
The Next Level Engineering described in this article enables companies to accelerate and improve the process of product and service development with technologies such as artificial intelligence, robot process automation (RPA), digital twins in engineering and virtual reality. All of these digital technologies complement the functions by adding in additional dimensions of adaptability. Not only do they increase the success rate of product and service innovations, they also help companies save time and money.
The outlined solutions are part of the overarching strategy we call OPERA. OPERA stands for Open up Operations, Perfect the value chain, Embrace digital, Reorchestrate value generation and Accelerate the learning game and is an overall strategic concept to describe the framework for future-proof Operations.
Contact our experts
Would you like to know more about how to take your company to the next level of engineering? Please don't hesitate to get in touch with our experts Carsten Bock and Laura Jacobey .