Find out which impact the semiconductor crisis has on automakers and which steps have to be taken now.


Bifurcation and relocalization – Disruptions in the market for semiconductor chemicals
By Robert Henske and Falk Meissner
The semiconductors market is growing, with significant strategic implications for chemicals suppliers
Semiconductors enable the current technological disruptions in many industries driven by electrification, digitalization, connectivity, and artificial intelligence (AI). The global semiconductor industry has grown to over USD 500 billion in annual revenue. The ongoing semiconductor crisis reemphasizes the importance of these components in modern technology.
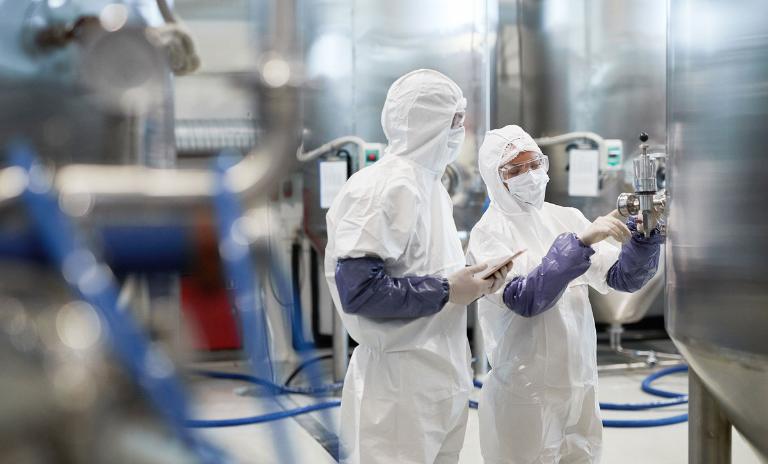
With USD 48 billion in sales in semiconductors, the chemicals industry has been a critical supplier to semiconductor manufacturing. Chemicals suppliers addressing the space have experienced high margins and growth driven by strong demand growth (6% per year), and the ever-increasing chemicals purity and specifications required in the race towards smaller nodes at the leading edge. This has limited the number of chemicals suppliers to a few highly sophisticated North American, European, and Japanese companies.
However, the semiconductor market is fundamentally changing, with significant strategic implications for chemicals suppliers.
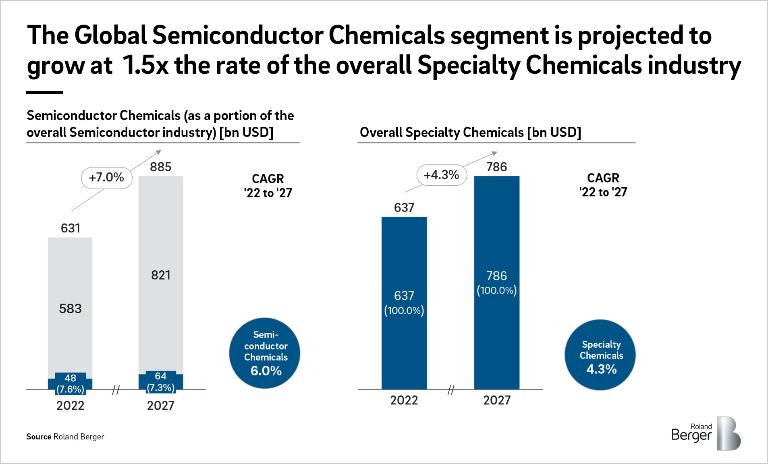
Bifurcation of semiconductor players
In the past, a large number of semiconductor players (TSMC, Samsung, Intel, Global Foundries, Texas Instruments, Infineon, and others) competed in the latest generations of nodes. Now, we see the semiconductor competitive landscape bifurcating.
Many historical semiconductor players such as Texas Instruments have opted out of the race towards the smallest nodes. They are focusing on next-to-leading or even legacy nodes.
The current semiconductor crisis reemphasized the need for capacity at the more legacy nodes. The automotive industry and many industrial applications still depend on much more legacy-driven electronic architectures. This bias drives a much higher dependency on next-to-leading and even legacy semiconductors for automotive controllers, power electronics, and sensors. This is in stark contrast to, say, mobile and consumer electronics, which use a much larger share of advanced semiconductor capacity for their centralized processors.
In these more legacy nodes, the democratization of technology is inviting other emerging players, such as new Chinese fabs, to compete. For these companies, the current available electronic chemicals and materials technologies are often deemed "good enough": There is limited need for continued improvement in purity and performance and there is limited need or appetite to pay for the most advanced technology. The definition and verification of specifications are increasingly being delegated to the fabs' direct suppliers, such as engineering players for fab construction materials, or distributors for sourcing of consumable chemicals and consumables. Conversely, technical service and security of supply are becoming much more important than product differentiation, as customers reduce in-house capabilities yet still seek to optimize costs.
Only a few leading-edge players like TSMC and Samsung continue to pursue smaller nodes beyond 5nm. These players have a need for continued chemicals and materials innovation to enable the higher levels of precision required with these smallest nodes. The cost of defects in manufacturing processes is so high that these customers continue to define and verify chemicals and materials specifications directly. That said, chemicals purity requirements may not continue to increase, as in many cases the "five 9s" purity levels (99.999%+) for chemicals far exceed the purity of other components in the semiconductor manufacturing process . To reduce contamination, other components like material handling piping/equipment, industrial gases, and assembly line metallurgy need to catch up to the standard set offered by leading chemicals suppliers in the space.
Relocalization of the semiconductor industry and supply chain
Over the last two decades, wafer fab capacity expansion moved from the traditional centers in Europe, Japan, and the US to Asia (specifically Korea, Taiwan, Singapore). Suppliers generally followed, building supply chain, manufacturing, and service capabilities in Asia.
Today, we are witnessing an emerging reemphasis on a domestic supply base in North America and Europe for wafer manufacturing, and consequently for the entire chemicals and consumables supply chain.
This trend began well before the current semiconductor crisis, as the US-China and Japan-Korea trade wars of 2018 and 2019 combined with long-term national defense concerns as well as increasing recognition of the strategic importance of semiconductors to critical economic sectors like telecommunications and automotive had led companies and governments to push for a rebalancing of the industry:
- Chip customers like Apple and Tesla, together with policymakers, pushed for new US fab builds, leading to TSMC's 2020 announcement that it would build a chip plant in Phoenix, Arizona, with the ability to make advanced nodes
- In late 2020, the European Commission issued a USD 145 billion semiconductor investment plan and proposed a European processor initiative to reestablish a European leading-edge high-performance CPU manufacturing base
- In early 2021, the US followed suit, passing the CHIPS Act to accelerate the rebuilding of American semiconductor manufacturing capacity, alongside placing increasing restrictions on the export and/or transfer of semiconductor products, equipment, and technology
- In mid-2022, US Congress plans to allocate USD 52 billion for semiconductor industry development as part of the China Competition Bill, to further support the US repatriation of semiconductor production
Since then, the semiconductor crisis has accelerated reshoring actions. Indeed, recent fab announcements indicate a resurgence of domestic capacity in the US: In 2021, Samsung announced a USD 17 billion plant in Texas, and TSMC is considering additional US plants beyond its initial Arizona fab. Intel recently announced a massive, EUR 33 billion investment in Magdeburg, Germany. Several other players are considering fabs for advanced nodes in North America and Europe as well. In the meantime, Taiwan, Korea, and Japan continue to invest in their semiconductor manufacturing base to defend their current leading positions. Suppliers along the value chain are following these investments and rebuilding capabilities in regions like the US or Germany that had seen their semiconductor industry declining.
The current Ukraine crisis will further accelerate this process, as it has demonstrated the global dependencies on semiconductor chemicals like Russian-supplied palladium, as well as Ukrainian-supplied semiconductor-grade neon gas across political boundaries.
China is leapfrogging semiconductor technology but still several years behind the leading players
China is a clear semiconductor chemicals industry leader long term, yet it is a wild card short term. In the last few years, the Chinese government has elevated the buildup of its domestic semiconductor industry to a critical level of strategic importance in its 5-year plans. While the Chinese semiconductor industry is still not yet at the leading edge, it is quickly catching up – it was 20 years behind just 3-5 years ago.
The Chinese government is strongly encouraging localization of the full supply chain, including electronics chemicals and materials. Many suppliers have obliged and built or are in the process of building capacity and supply networks to serve Chinese customers with Chinese-made products.
Value chain steps with lower technology barriers (like conversion of polymers into parts) will localize faster than steps requiring deep expertise, like high-purity reaction processes.
All of these changes in the semiconductor industry raise key strategic questions for chemicals and materials suppliers:
Question #1: Is my offering aligned with the new bifurcating demands of leading-edge vs. legacy nodes?
- Do I have the R&D capabilities to support leading-edge nodes? Is there a clear ROI for chemicals and materials suppliers on meeting the next level of specification?
- Do I have the service and supply security capabilities to support legacy nodes?
- Do I have the resources to maintain my market share in legacy nodes while pursuing growth in leading-edge nodes?
Question #2: Is my global footprint aligned with the future global semiconductor order?
- Do I have the right North American and European assets to support new fabs in these regions?
- Do I have the right Asian footprint to serve the Korean and Taiwanese supply chains?
Question #3: Do I have a clear China strategy?
- Do I have clarity as to what to make in China vs. import from other regions?
- Do I have the right relationships and channels to participate in the accelerated growth of local players?
These questions have become more urgent and more complicated with recent events. Finding the answers is crucial to maintain a competitive position within the semiconductor chemicals supply chain.
Conclusion
Geopolitical developments have changed the landscape of the global semiconductor space, and there are likely to be unpredictable geopolitical developments that will impact this space down the line as well. The investment decisions of leading industry players and the governments that house their production processes point to a continued bifurcation within the industry as well as industry and supply chain relocalization.
Bifurcation has been driven by a growing gap in the precision and purity requirements of chip customers; some leading industry players are content to cater to legacy nodes, whereas others are deep in the race towards selling ever-smaller and purer nodes to support advanced products. By contrast, relocalization has been driven by long-simmering trade wars, long-term national defense concerns, and increasing recognition of the strategic importance of semiconductors to critical economic sectors. Furthermore, geopolitics has impacted and will keep impacting relocalization, as the current Ukraine crisis shows only too clearly.
Given these developments, chemicals and materials suppliers must pose and answer key strategic questions to align their offerings and footprint with the future of the semiconductor space. And looming in the background lies the proverbial elephant in the room, the country whose ambitions and decisions will shape the industry more than any other going forward: China. Responding to these challenges is crucial to maintain a competitive position within the semiconductor chemicals supply chain.
The authors would like to thank Brag Selvarajan for his significant contribution to this paper.
Sign up for our newsletter and get regular updates on Automotive topics.