Learn more about the MIH Alliance and their plan to build an open source platform for electric vehicles and how smaller automobile manufacturers might benefit.


Meet the automotive disrupters: Building tomorrow's battery today
An interview with Doug Campbell, co-founder and CEO of Solid Power
"With the advantages of higher energy, improved safety and extended calendar life, we expect a lower-priced battery both at the cell-level and at the pack level."
Doug Campbell is co-founder and CEO of Solid Power, an industry-leading producer of all-solid-state batteries for electric vehicles. Solid Power is backed by prominent investors including Ford, BMW, Hyundai, Samsung, and more.
Roland Berger Partner Wolfgang Bernhart recently spoke with Campbell about his company's USD 1.2 billion valuation, what distinguishes his battery technology from others, and how Solid Power impacts the supply chain.
In this insightful interview (edited for clarity), Campbell explains his partnerships with leading automotive brands, how sulfide solid electrolytes can significantly improve safety and reduce the cost of batteries, and how his business model works for the future of electric vehicles.
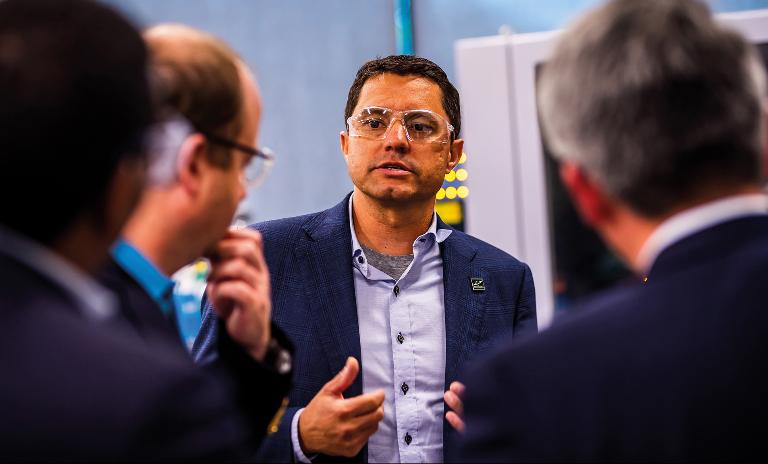
What are the advantages of your all-solid-state batteries when compared to others on the market?
Four things: higher energy density, improved safety, extended calendar life and lower costs.
We expect to reach significantly higher energy densities of more than 400 Wh per kg and near 1,000 Wh/l, which is significantly more than what can be achieved today in lithium-ion cells. This is due to the high energy electrodes that are enabled in our all-solid-state platform, including high-content silicon and lithium metal anodes.
With better safety and character life characteristics, we could eliminate the need for pack cooling leading to simpler pack designs, which could significantly reduce battery pack costs. By eliminating the liquid electrolyte, we reduce the chance of thermal runaway and other negative side reactions that otherwise occur in lithium-ion batteries. Our technology also allows us to extend battery life even when exposed to higher temperatures. In our testing, even at 70 degrees Celsius, we haven't seen any irreversible capacity loss in our batteries when compared to standard lithium-ion batteries.
With the advantages of higher energy, improved safety and extended calendar life, we expect a lower-priced battery both at the cell-level and at the pack level. Our OEM partners believe we can overcome many of the problems that have so far prevented lithium-ion batteries from reaching their potential when it comes to powering electric vehicles.
As of now, we've already demonstrated compliance with automotive requirements using a Si-anode, which includes more than 50% silicon content by weight. Therefore, we target the Si-anode for our first commercial applications. With Li-metal, we still have requirements to meet, but our testing so far has demonstrated excellent results, so we're trending in the right direction.
What are the next steps to achieve the higher energy densities you are targeting?
It is all about process optimization, scale, and larger cells. Going to 100 Ah will significantly improve energy density. We will have less parasitic losses. For example, our current separator is relatively thick at 50 microns; with Li-metal we reduce the thickness to 30 microns, and with a silicon anode we can achieve an even thinner separator layer.
What other challenges are you currently facing, and will the introduction of your technology render existing cell production capacity useless?
This goes back to the founding of our company and the strategy we established. That is, we did not want to reinvent the wheel. In fact, we designed the chemistry in a way that existing manufacturing facilities can be used, and conversion costs can be kept as low as 5–10% of initial investments. You will see most of the same equipment in Solid Power’s facilities that you would in today's lithium-ion gigafactories. Both the solid electrolyte and Li-metal foils can be handled in conventional dry rooms with a -40 degree Celsius dew point. And we do not require formation equipment. So no, we have not rendered existing production useless, but we're greatly improving it.
In fact, Solid Power can also leverage most of the existing supply chains for battery materials. But there are two supply chains we need to build: the supply of both Li-metal anodes and Li-sulfide, neither of which are produced in large enough quantities right now. Our strategy here is twofold. We're depending on our supply chain partners to make the necessary investments needed to scale production and bring costs down, especially for the Li-metal foil. We expect that Li-metal foil will only have a small cost premium compared to lithium ingots. For the lithium sulfide, lithium hydroxide is combined with hydrogen sulfide gas. Here we are going for both inhouse production and production with an industrial partner.
But based on our extremely in-depth discussions and investigations, we've concluded that there's nothing inherently expensive about our technology. What's more, we believe that our cost of goods sold will continue to decline when tracked to similar materials that are becoming more affordable. In some cases, our material sourcing could become extremely affordable.
Once we scale our production, we're confident the cost of our materials will drop precipitously to get to around USD 85 per kilowatt per hour at the cell level for an NCM811 cell. We will basically have a similar cost profile to current Li-ion cells, that is, dominated by the cost of the cathode materials. The justification will be the cost advantages on the pack level, simpler pack designs, and lower risks for future product recalls. OEMs are already developing these next stage platform designs.
You plan to be on the market and in vehicles by 2026. How will your business model work by then?
We will license our cell technology to commercialization partners like a tier-1 cell supplier. From the beginning, we knew we didn't want to become cell producers given their high risk profile, massive capital investment, and thin profit margins. We didn't want to directly compete with Panasonic, LG, and others. So stepping into an existing gigafactory as a material and technology partner affords us the option of leveraging existing investments. That's not to say we don't or won't have competitors. But by this time next year, we will be producing larger volumes of electrolyte material than anyone else in the sulfide electrolyte space.
In short, our licensing approach allows us to become a more profitable business much more quickly without the need for significant capital investment. Production of the solid electrolytes is several orders of magnitude less CAPEX intensive than cell manufacturing, and standard industry margins are higher, in the range of 15% to 20%.
Thanks for spending time with us, Doug.
Sign up for our newsletter and get regular updates on Automotive topics.
Campbell co-founded Solid Power in 2012 while simultaneously co-founding what eventually became Roccor, an industry leader in providing components into the small satellite industry. He led both companies as CEO through 2018, after which he transitioned to Board Chairman at Roccor, where he guided the company through an acquisition by RedWire Space in late 2020.