Operating processes are currently undergoing disruptive change. Learn here how to adapt your company's operating processes to the future.
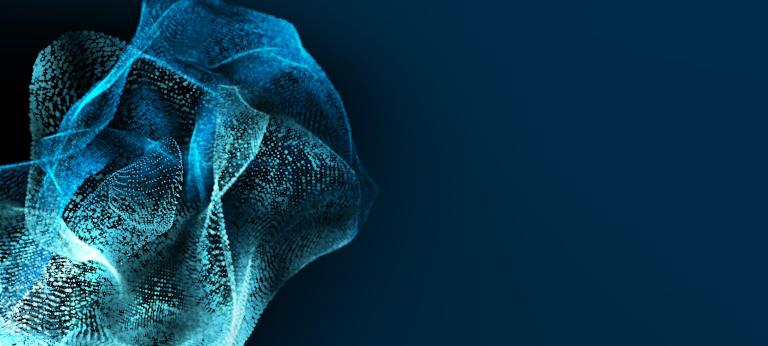

Tackling labor scarcity in the manufacturing industry
How Roland Berger can help organisations to close the skills gap
There are numerous factors contributing to the problem, including: a decline in the working-age population; reduced attractiveness of production jobs; the increasing complexity of digitalization; and global competition for skilled workers. This poses a serious question: How can manufacturing companies cope with this threat and secure their future workforce?
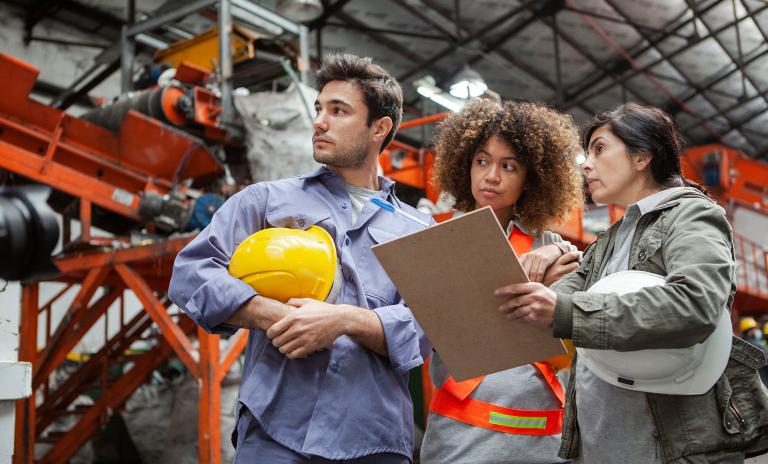
Understanding the causes and effects of labor scarcity
Labor scarcity is the situation where the demand for labor exceeds the supply, resulting in difficulties to fill vacancies, and thus to fully deliver business goals and to drive growth. According to a survey by the ifo Institute, 57% of metalworking companies in Germany reported operational difficulties due to staffing shortages in 2022, and the average time to fill a position was four months. The situation is expected to worsen in the coming years with the working-age population in the EU projected to decline 10% by 2050. Meanwhile, other regions such as India, the US, and Sub-Saharan Africa will see their workforces grow.
Labor scarcity affects the manufacturing industry more than other sectors, as production jobs often require specific technical skills, physical presence, and exposure to challenging working conditions. Production jobs are also less attractive to the younger generation, who prefer more flexible, creative, and digitally oriented careers. As a result, manufacturing companies face a higher risk of losing their competitiveness, innovation, and growth potential as well as their ability to meet customer demands and quality standards if, for example, they cannot find enough qualified welders, lathe operators, milling cutters or staff with lean production skills.
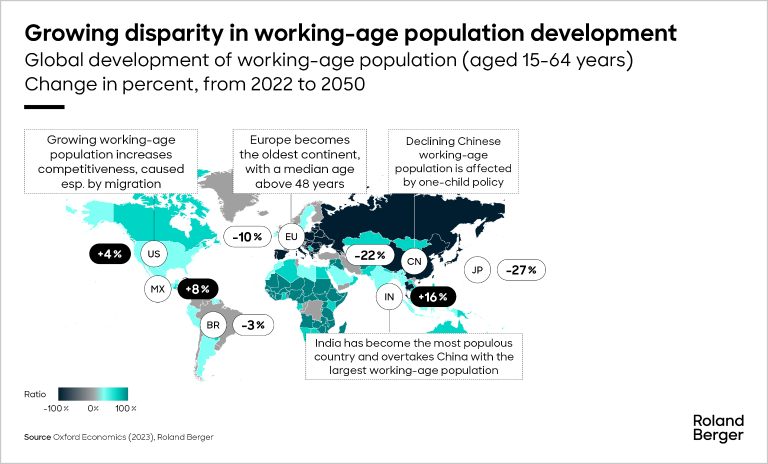
Assessing the vulnerability and potential of each company
Not all manufacturing companies are equally vulnerable to labor scarcity, nor do they have the same potential to reduce its impact. It is crucial for each company to identify the areas in which it needs to take action.
Roland Berger has developed a four-step approach to help manufacturing companies deal with labor scarcity.
- Step 1: Assess the company's vulnerability towards labor scarcity. This involves analyzing the key workforce supply and demand metrics such as the current age distribution, fluctuation, and employee projection of the workforce as well as mapping the regional demographics and competition around production sites. Understanding your skill demand is a vital factor: Define and forecast requirements, both in the short term as well as in five-plus years’ time. This is the true center of workforce management and one of the most challenging management tasks. RB will help with functional (work force management approach) and industry knowhow future skills.
- Step 2: Assess labor scarcity focus areas and identify potential gaps. This step includes several assessment areas such as: automatization potential, operational processes, organizational setup and talent management, as well as value-chain coverage and business models. It will look to capture to collect initiatives and measures to improve productivity, efficiency, flexibility, and attractiveness.
- Step 3: Create a labor scarcity matrix. This establishes a rating on a company level as well as a breakdown of further functions to identify where tailored measures are needed.
- Step 4: Select and prioritize measures. Based on the previous steps, a company can derive and evaluate measures to reduce its vulnerability toward labor scarcity. These may include increasing automation, attracting more workers, relocating production sites , or outsourcing production steps.
This approach isn't just about patching up holes ― it's about reimagining the workforce lifecycle. From recruitment to retirement, each stage offers opportunities for innovation and improvement. By adapting to the global dynamics of the labor market, companies can ensure they're not just surviving but thriving in the face of labor scarcity.
Leveraging Roland Berger’s expertise and tools
Roland Berger has a unique expertise and a proven set of tools to support manufacturing companies in their labor scarcity assessment and mitigation. With our combination of industry and functional know-how, Roland Berger can help companies to strategically manage their workforce, close their skills gaps, and increase their resilience and competitiveness. Some of the tools and methods we offer include:
- Workforce Management Approach: A tool to extrapolate the workforce supply and demand, identify the gaps and risks, and derive the necessary actions.
- Rapid Plant Assessment: A tool to increase the transparency of the personnel resource allocation and potential improvements.
- Industry 4.0 Assessment: A framework to identify and evaluate use cases for the digitalization of manufacturing.
- Production Footprint Toolset: A tool to find the optimal location and value stream allocation for the production network.
- Lever Checklist: A checklist of potential measures to reduce labor scarcity, ranging from automation and lean production to talent acquisition and retention.
By applying these tools and methods, Roland Berger can help manufacturing companies transform their workforce and production system, and to overcome the challenge of labor scarcity.
We would like to thank Tim Femmer for co-authoring this article.