Roland Berger's NGM country radar helps production strategists to capitalize on the trends sweeping across the manufacturing industry
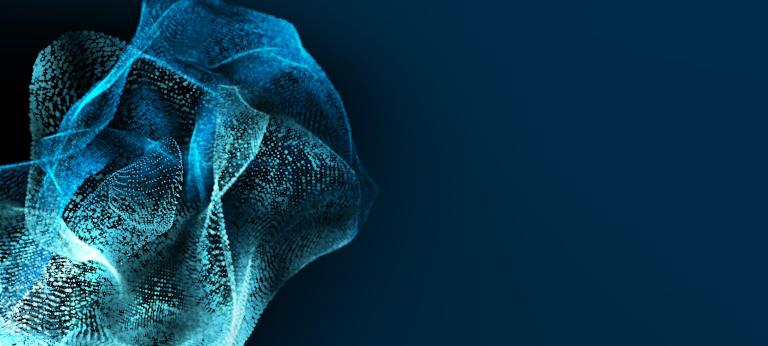

Location matters
By Oliver Knapp and Bernhard Langefeld
Where to manufacture in a new world?
In a world where many global value chains no longer function seamlessly, manufacturing companies are rethinking their production location strategies. Companies must make choices about their manufacturing locations an essential part of their corporate strategy, tailored to individual customer benefits and the company's own targets. Roland Berger’s Next Generation Manufacturing toolset helps companies adjust their manufacturing footprint.

The vision of a perfect globalized world is broken: Between 2005 and 2019, Asia's share of global "value add" in manufacturing grew by 15 percentage points, while Europe and the Americas expanded at below-average rates. But over the last three to four years, increasing geopolitical tensions, combined with crises such as the COVID-19 pandemic, have disrupted international supply chains and put the brakes on globalization.
In this world steering towards “decoupling”, where many global value chains no longer function seamlessly and traditional interdependences between nations are weakened, manufacturing companies are now rethinking their production location strategies. We can already observe the end of the massive shift of production to China, with many companies currently considering "near-shoring" or "friend-shoring" – shifting production to their home country or nearby locations. With around USD 1.5 trillion “value add” in manufacturing at stake globally, by 2030, the question of where tomorrow's production should take place is more relevant than ever.
Location matters – as identified by the authors of Roland Berger's Next Generation Manufacturing Framework. Our experts include location as one of the megatrends affecting companies, alongside five other factors: sustainability, industry disruption, individualization, populism, and digitalization. Manufacturing companies can choose to ignore these megatrends and risk seeing their competitiveness wane, or they can proactively leverage them and turn manufacturing from a perceived liability into a true asset.
"Traditional site selection criteria are no longer adequate. The site selection criteria have broadened, and our Next Generation Manufacturing is a perfect way to look beyond cost and labor factors."
Winners and losers
Adjusted for average regional growth, manufacturing in traditional countries such as Germany, Japan and the United Kingdom grew at below-average rates from 2015 to 2019, partially because manufacturing value-add was shifted to lower-cost countries. Now, the shifting trend appears to have reversed. Since 2018, some 63 % of the world's largest manufacturing companies have changed (or announced changes to) their production footprint. Of these companies, 52 % have shifted production to their home or neighboring countries. The reasons most frequently cited are customer proximity, reduced supply-chain risks and increased sustainability due to reduced transport emissions. Of those companies that have changed their footprint, 70 % have built or are now building production facilities on greenfield sites, while 22 % are realizing both greenfield and brownfield site projects. The remaining one percent have either extended their existing facilities or closed sites down.
Criteria for selecting sites
Adjusting your manufacturing footprint is a major decision – indeed, it is often one of the biggest decisions a CEO ever makes, and one that can take years to fully implement. A solid basis for this momentous decision is needed, taking into account specific features of the company and its legacy production network. It is not a decision purely for the "manufacturing" side or the COO.
Traditional site selection criteria are no longer adequate. To broaden companies' perspectives, Roland Berger takes a wide range of site selection criteria, grouping them under the six major trends (without individualization) based on our Next Generation Manufacturing framework . These selection criteria, while not exhaustive, look beyond traditional factors such as costs, subsidies and labor, and include factors such as regional legislation, industry-specific trends, customer awareness, and so on. New site selection criteria should also take the company's specific position and its production legacy into account.
Of course, megatrends do not affect all countries equally: Some are more relevant in certain regions than in others. We have therefore developed the Next Generation Manufacturing country radar , which includes 26 different indicators based on data from 58 countries across five continents. The country radar provides companies with an overview of the status of the megatrends in different countries, helping them make informed decisions about their future manufacturing footprint.
"Adjusting your manufacturing footprint takes time, but companies can take several steps at an early stage that ultimately contribute to the success of the relocation."
Production network archetypes
In a world steering towards decoupling, the range of types – or "archetypes" – of production networks differs significantly from those in a globalized world. At one end of the spectrum, we have a fully globalized archetype; at the other, a "local-for-local" or "region-for-region" archetype, in which companies have a factory in each major region, supplying local customers and providing greater customer proximity, lower supply-chain risks and reduced transportation costs and emissions.
The latter archetype is only feasible for major companies, which enjoy a certain scale, legacy production footprint and the economic resources required for the greater administrative and investment costs involved. Some companies may choose a "critical-parts nearshorer" archetype, for example, producing critical parts in a risk-averse production country and the remaining parts in best-cost countries. Or they may choose a "local production with global export" archetype, closely tailored to their own needs.
First steps
Adjusting your manufacturing footprint takes time: Even relocating the production of a single product requires meticulous preparations, including planning the transportation of machinery, adaptations to infrastructure, building up stock, and so on. Companies can take several steps at an early stage that ultimately contribute to the success of the relocation. For example, "production wargaming" is an effective tool for speeding up decisions and avoiding drawn-out meetings and data-gathering projects. Scenario options, automated data-gathering and a "war-room engine" calculating different scenario outputs, such as product flows, footprint impact and capacity plans, all help enable fast, fact-based decision-making. Setting up a geopolitical and crisis monitoring "watch tower" is also an effective way to manage unexpected events and handle them in a coordinated manner without overwhelming the organization with ad hoc crisis meetings.
A number of other steps can ensure adaptability, such as flexible production lines, certification of multiple sites for one product, digital production/product instructions, digital expertise bases or even partial outsourcing to manufacturing-as-a-service providers. These options can be used to mitigate risks, buffer increased capital expenditure on investments and overcome capacity constraints. Indeed, they make it possible to rethink production entirely.
In conclusion
The future competitiveness of manufacturing companies will increasingly be determined by their manufacturing footprint. At the same time, decisions about that footprint are becoming more complex, with important new trends emerging. Companies must make choices about their manufacturing locations an essential part of their corporate strategy, tailored to individual customer benefits and the company's own targets.
Interested in exploring how our Next Generation Manufacturing tools can help you successfully choose a new manufacturing site? Download our use case below for an example. Our operations experts would be happy to discuss the topic in more depth.
Register now to download the full PDF including key insights, new developments as well as future challenges and new opportunities for players the manufacturing industry.