Elevate your business with our automobile consulting services. We provide expert advice, tailored for industry professionals seeking efficiency.
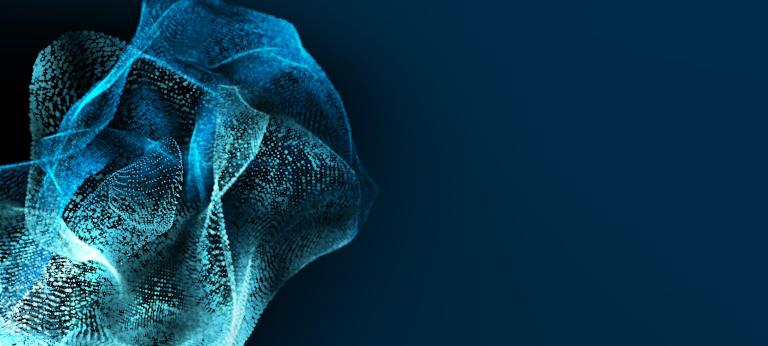

Automotive industry: Transformation through partnerships
OEMs and auto suppliers will only master crises, supply crunches and rising costs if they work together
Transformation remains the constant theme for the automotive industry. In the face of the transition to electric mobility in a volatile, uncertain, complex and ambiguous world, partnerships between OEMs and auto suppliers are nothing less than vital. Only by working together can the industry's players emerge from the transformation as a profitable business with the flexibility to adapt to the conditions before them.
Mobility in Motion, a special supplement we put together for Automobilwoche, highlights the key challenges and solution strategies for a successful transformation.
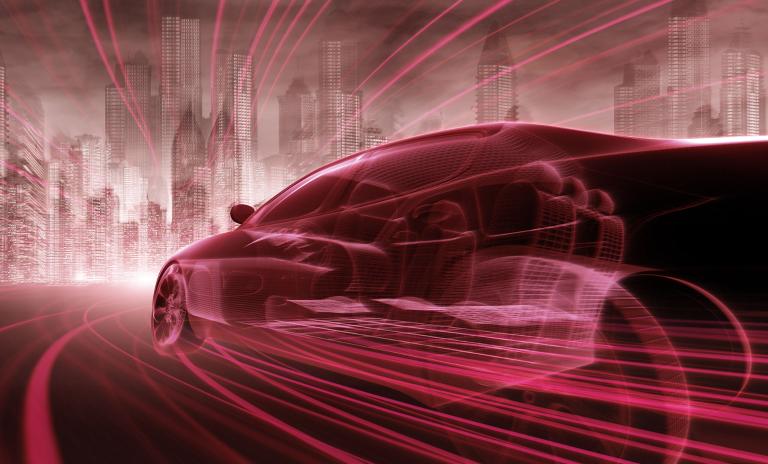
OEMs and automotive suppliers should work together to halt the increase in costs
Growing technical complexity, electrification, digitalization: Numerous factors are driving vehicle costs ever upward. If cars are to remain affordable and generate the necessary margins, it is vital to keep the increase in costs to a minimum by optimizing the entire value chain. OEMs and auto suppliers will need to work together, each doing what they can to help achieve this. For example, closer collaboration in component development can reduce costs and specifications. Designing less complex components that are not brand specific, which suppliers can then adapt for different customers with limited effort, will bring savings through economies of scale. And transparency can increase efficiency: If OEMs present their technology roadmaps clearly, suppliers will have an idea of which solutions have a chance of going into series production.
Rethink production from the ground up
Automotive industry players should use the current polycrisis – defined as a situation with several catastrophic events occurring at once – as a chance to fundamentally rethink their product and production strategies. The shift to electric vehicles is a good opportunity for companies to review their vertical integration. Product variance can account for one-fifth of total production costs. With fewer product and equipment variants at a given plant, OEMs can significantly reduce their production control and process complexity and thus manufacture more cost effectively.
While industry incumbents face the challenge of having to master the existing product complexity, automotive newcomers benefit greatly from the fact that they can go right back to the drawing board for their model development.
"The automotive industry must use the profound transformation that is currently ongoing as an opportunity to fundamentally rethink its value creation strategies and streamline them for performance."
Margin pressure continues for suppliers
Since as far back as 2019, OEMs' and suppliers' margins have been moving in opposite directions: up for OEMs and down for traditional suppliers – partly because most suppliers have been unable to pass through the full extent of the rising costs for energy, materials and logistics and the effects of the chip shortages. Their margins fell from 5.3% in 2021 to 4.6% in 2022 on average. In 2017, margins had been up at 7.5%.
Growth is taking place primarily in the electric powertrain, especially in batteries, and in digitalization. But profitability also depends on a company's position in the supply chain. Because OEMs were able to channel scarce parts into their products with the highest margins and also push through higher prices, profits for raw material producers, chip suppliers and transport companies have been high. Tier-1 and Tier-2 suppliers, on the other hand, were only able to pass on part of their increased expenditure to the OEMs, so their margins have suffered more. Suppliers of standard parts and commodities will have to concentrate on even more efficient production. They should also look into whether they can generate revenues in other sectors with the products and competencies they have.
Mitigating risk must take precedence
To operate successfully in a volatile, uncertain, complex and ambiguous (VUCA) world, all players must put their risk management on a much broader footing and plan for the various possible scenarios.
If they assume that the political environment in a country is going to deteriorate, for example, they can choose the option of de-risking, whereby they might increase inventories or set up alternative warehouses. Capsulation is suitable if they fear a crisis of longer duration. In this case, they should take preventive measures – such as already making production and sourcing not dependent on this region – and only switching to decoupling, the last stage prior to exit, as and when the crisis actually occurs.
“Being open to other providers is key”
In his interview, Sven Schuwirth, CUPRA COO, talks about the new challenges facing incumbent automakers. His key message is that OEMs and suppliers should partner up where it makes sense. He also believes that the industry in Europe can make itself future-proof: "We need to shore up our strengths, particularly in design, branding and all-round experience, as well as in classic parameters such as the chassis, or comfort. We'll be able to do that as long as we don't try to do everything ourselves but look instead to more collaboration and more alliances and focus on what we are really good at, which is a lot."
Sustainability: The circular economy as an important decarbonization lever
Unlike internal combustion vehicles, electric cars produce the majority of their carbon footprint not in production but in the upstream value chain, starting with the raw material extraction. Product design, supply chain, raw materials and country of origin are the primary channels for influencing Scope 3 upstream emissions.
The circular economy is a sustainability strategy that defines new paradigms for material flows and requires new supply chains to be built. What it offers in return is not only a lesser impact on the environment but another advantage too: Recycling promises greater independence from rising raw material prices and shortages.
Indeed, circular approaches offer good ways of reducing costs, limiting the consumption of scarce raw materials and mitigating the carbon footprint of components like batteries. There are three fundamental options: material recycling by taking the battery apart and recovering the raw materials, second-life applications whereby old batteries are used for instance for stationary energy storage, and remanufacturing batteries so that they can be reinstalled in vehicles as spares.
Because efforts towards a circular economy will only pay off in the fairly long term, OEMs and auto suppliers should act fast to develop and deliver strategies for decarbonization and the circular economy.
The outlined aspects are just a snapshot of the issues facing automotive today and some of the ways of solving them. Download Mobility in Motion, our special supplement for Automobilwoche, to read more about how the automotive industry can achieve a successful transformation.
Register now to download "Mobility in Motion", a special supplement we realized together with "Automobilwoche".