Roland Berger has developed a wide range of future-oriented consulting services for manufacturers on the road to Next Generation Manufacturing.
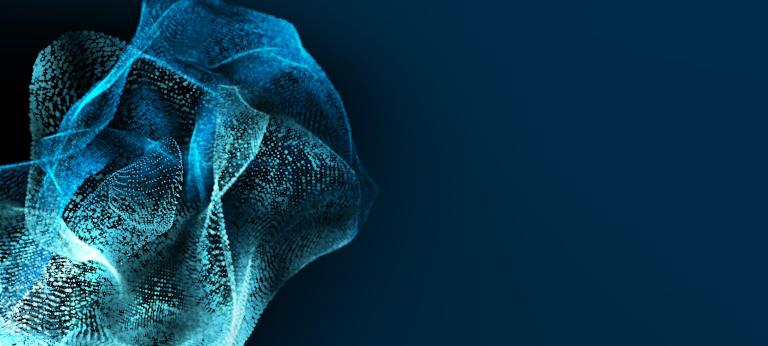

Reviving production with Next Generation Manufacturing
Global trends spark paradigm shift in manufacturing and offer opportunities to be more competitive
With over 6,500 companies, around a million employees and revenues topping EUR 220 billion, Germany's engineering sector is the country's largest industrial sector after the automotive industry. But it, too, is experiencing a transformation as a result of global developments: disrupted supply chains and rising logistics costs; changing demands from customers, investors and legislators around sustainability and production locations; greater demand for individualized products; technology disruptions – the factors affecting engineering companies are many and varied. All of these trends require businesses to make adjustments in order to avoid a slow and steady decline. Yet at the same time, they also offer an opportunity to transform the industry and put manufacturing on a new footing. Against this backdrop, the German engineering association VDMA and Roland Berger conducted a survey among VDMA members to assess the mood in the German engineering sector. The results indicate that the traditional levers for reducing costs and increasing efficiency have in many cases been exhausted, but there are new approaches that can be used to draw on today's disruptive trends to position the industry for the future.

With its high export share and large numbers of suppliers all over the world, Germany's engineering sector benefited from global trade for decades. Low logistics costs and well-established supply chains allowed companies to escape everyday cost and efficiency pressures by relocating production facilities to low-wage countries and increasing productivity in their own manufacturing manufacturing operations through greater automation, optimization and methods such as lean manufacturing. But the system has recently been challenged by a series of developments that make "business as usual" simply impossible. Central to this are the effects of six key trends that are driving the transformation:
- Sustainability is becoming increasingly important and is demanded by consumers, investors and governments alike.
- Technology disruptions such as the coming end of fossil fuel drivetrains and power generation technologies are calling entire business models into question.
- Production localization is becoming more important as transport and logistics costs and supply chain risks increase, and local manufacturing is desired by customers and demanded by governments.
- Individualization and one-off products are increasingly in demand and are creating more complexity in manufacturing.
- Populism is an issue in more and more countries, forcing many companies to pay more attention to the way they and their products are perceived by the public and be more careful about the setup of their production network.
- Digitalization and Industry 4.0 have passed the point of no return and are now ever more important in industrial production.
All of these developments are pointing in one direction and require manufacturing companies to make adjustments. On the other hand, they also offer manufacturers a unique opportunity to transform their industry and take production to a new level.
"With NGM, companies can transform manufacturing from a 'chore' into a value driver and crucial competitive advantage."
Companies expect cost pressure in production to rise further
The survey by Roland Berger and the VDMA paints a clear picture: 80% of engineering companies admit that their production operations face permanently high pressure to achieve cost reductions and manufacturing efficiency ; 64% expect the pressure to increase further in the future (slider image 1). Companies in the drivetrains sector feel hardest hit, having less potential for differentiation and therefore facing greater (price) competition.
The surveyed companies have mainly used traditional levers to counteract cost and efficiency pressures to date: They take steps to achieve further process optimization and automation, outsource selected manufacturing processes or relocate them to low-wage countries, intensify lean manufacturing, and so on (slider image 2). But it is also apparent that more and more companies have recognized that the "old world" is no more: The majority of survey respondents state that it is increasingly difficult to achieve further progress with traditional methods – they have exhausted the potential of the levers they used to use. What is more, if all companies in the market rely on the same optimization toolset, opportunities for differentiation will be scarce: Only 7 percent of respondents see any scope at all for differentiation.
Next Generation Manufacturing as a way out of the impasse
These and other survey findings show that manufacturing companies need to find new ways to break out of the Catch-22 that is the old world. Roland Berger has developed the concept of Next Generation Manufacturing (NGM) to help: Companies can use it to come up with individually suitable measures within the six trend clusters to deal with the new challenges they face. NGM is based on a new way of thinking about manufacturing and comprises a whole host of approaches that companies can adopt to open up the new world, a world in which manufacturing is not a chore but a value driver and a crucial competitive advantage.
Many companies have already spotted the potential this offers: 59% of survey participants see opportunities to become more competitive by considering the six NGM trends in their production strategy. A total of 57% believe this will enable them to rethink their manufacturing and put it on a new footing. However, many still feel uncertain: Less than a quarter of firms consider themselves to be on a good footing and believe they can play a pioneering role in the NGM context. One thing that is missing is the right framework in terms of government policies: 68% of the companies surveyed do not believe the right framework is in place. Key shortcomings are seen on a legal level, such as intellectual property protections, anti-corruption measures and the reduction of red tape; on a technical level, such as access to high-speed Internet, a stable power grid and suitable transport infrastructure; and on a tax level, such as import/export duties, government funded research and income taxes; other issues are also seen to be less than ideal, including the education system and the shortage of qualified talents entering the industry, as well as public safety (slider image 4).
Best practices prove the potential of NGM
As part of the study, the experts from Roland Berger and the VDMA also conducted extensive interviews with companies that are considered pioneers in the field of NGM. These made it very clear that the concept is not a standardized system but rather a diverse toolbox from which companies must each select the individual elements that best suit their own needs and implement them in the way that's right for them. A leading global plant manufacturer, for example, focused primarily on the digitalization trend and digitally integrated its entire value chain from suppliers to assembly to aftersales service. Order processes are now automated and handled digitally – with around 1,000 suppliers and 600 million parts per year, this results in a considerable efficiency gain.
Another company, a pump manufacturer with a long tradition, built a brand new smart factory at its German headquarters over the past seven years to strengthen its German production operations. Besides the buildings and infrastructure being optimized for sustainability, production processes were also reorganized with this aspect in mind: From the planning of customer orders to automated production and dynamic logistics to supplier integration, all processes are now digitalized from end to end. This permits a flexible reaction to any changes in demand, and customers can even configure their own individual product online, order it at the touch of a button and thus trigger the automated production process. Just over two years since the completion of the new smart factory, material and inventory levels have been reduced and production times shortened – while productivity is around 10% higher.
The joint study by VDMA and Roland Berger featuring further findings as well as the practical case studies is expected to be published later this year.
Register now to receive regular insights on Next Generation Manufacturing.